Repair Taxiway Bravo Ramp (WAK008) and Repair Hot Cargo Pad (WAK006)
Project Summary
Southwest Concrete Paving (SWCP) served as key subcontractor for the Repair Hot Cargo Pad and Repair Bravo Taxiway (WAK006 & WAK008). The project was awarded as a design-build project to AECOM and included two different sites on a military base at Wake Island. The USAF maintains an active base on Wake Island, a tiny atoll island located approximately 2,500 miles west of Hawaii. The base encompasses the entire island, with access to the island restricted to those actively stationed on base or federal contractors working on active projects. Travel to the project location itself was a long and cumbersome journey that required a chartered flight from Honolulu to the island, typically a 4-5 hour flight. These flights, scheduled only every two weeks, brought in a limited number of supplies along with a fresh crew while another crew departed off the island to return home for a short break. The airfield consists of a 10,000-foot-long runway and an adjacent taxiway, Taxiway Echo (E). Taxiway Bravo (B) is adjacent to the main Taxiway E and connects at the other end of Taxiway B to Taxiway Alpha (A). Just off Taxiway E, on the other end of the runway, is the Hot Cargo Pad, which is used as a parking/staging area for aircraft carrying hazardous cargo. The project involved replacing the existing asphalt on both Taxiway B and the Hot Cargo Pad with heavy-duty airfield Portland concrete cement pavement (PCCP). Due to the extreme remoteness of the project, SWCP carefully planned every aspect of the project to ensure that the project was a success. Most of the project materials needed to be barged in from the mainland U.S., including all aggregates and required material for construction and temporary housing, construction and batching equipment, and a water filtration system for construction water and the batch plant. SWCP was highly cautious with the quantities, not exceeding the allocated materials and not bringing excess material due to the remote location and subsequent costs.
SWCP utilized a GOMACO 9500 equipped with a trimmer head and a Leica Stringless 3D system to maintain quantities and make a final cut on our subgrade before laying PCCP. However, as paving operations began and the GOMACO 9500 was needed as a placer, SWCP could better utilize the motor grader to finely grade the subgrade before paving.
Along with demolishing the existing asphalt taxiway and Hot Cargo Pad, the subgrade, mainly of native soil and crushed seashells, had to be mechanically stabilized. The batch plant location was on the base, just off the airfield, which already had limited access. Having the batch plant so close to the Taxiway B project location meant a quick turnaround at the plant. The hauling time significantly increased once PCCP on Taxiway B was completed and paving operations moved towards the Hot Cargo Pad. Fortunately, SWCP was able to coordinate with personnel and other construction operations on base to maintain a reasonable traffic plan.
Most paving activities took place at night to reduce interference with airfield operations. However, to counteract the effects of the constant rain and weather delays, construction crews ran continuously for 24 hours, rotating between a day crew for grade preparation and clean up and a night crew for concrete paving operations. SWCP superintendents often worked longshifts to ensure a proper hand-off from the day crew to the night crew and vice versa. This seamless transition relied on precise scheduling, constant contact with airfield operations, and diesel-powered light plants at night. In addition to the new PCCP for the taxiway and Hot Cargo Pad, a PCCP shoulder was also placed. Upon completion, grounding rods and tie-downs were installed along both project areas for various aircraft. The work scope also included the removal and reconstruction of a dual 24-inch RCP storm drain line which connected the main drainage basin from the airfield to the bayside of the ocean, an electrical lighting system, and the final step striping the new PCCP
On-Site Batch Plant
SWCP mobilized a low-profile batch plant to set up on the island. The low pro-plant was selected because of its self-erect capability, which did not require a crane for erection. Despite this option, SWCP chose to fabricate and install a 4-foot riser on the plant requiring a small on-island crane to set the drum. All cementitious materials were mobilized to the site in one phase. These products were transported in super sacks, and the entire project was paved using sack unloaders to transfer cementitious material from the super sacks to on-site storage guppies.
Sustainability Measures, Including Economic and Environmental Factors:
Because of the project's remote island location, waste had to be carefully captured and boxed for return and disposal on the mainland. The ternary cement used on the project was significantly more environmentally friendly than typical cement. The combination of 15% limestone and 50% slag into the blend significantly minimized the amount of type II cement and significantly reduced the carbon footprint required in the manufacturing process. The utilization of on-site coral as the bedding and base material was an effective means of constructing the project.
Unique and Innovative Measures Employed by SWCP include:
•Stringless slip-form paving technology with the Wirtgen SP 94i with 20’ wide paving lanes reduced job site congestion and improved both horizontal and vertical concrete placement control.
• A 12-CY Rexcon Model S Central Mix Plant, which provided the highest quality concrete for this project.
• Coordination of activities with base personnel to maintain active airfield operations.
• Paving for the project was done primarily in the spring and summer season, although temperature fluxuation remained relatively low between seasons and did not play a role in concreting operations. The most significant impact to the schedule was rain. As this project is located in a tropical location which can provide more than 30 inches of rainfall in the rainy season, from April to November. It was typical to receive some rain almost every day.
• Using bag unloaders for cement dispersion was a challenge throughout the job. A separate shift had to be utilized each day to prepare for the paving shift in order to unload sufficient material to maintain schedule.
Unique Challenges / Solutions:
During our pavement operations planning process, SWCP worked closely with the on-site AECOM management as well as the Iowa-based design team to overcome challenges on the project. Working with and having a great relationship with the designer, SWCP provided a more suitable design and a better finish product for the customer. This better-quality product required substantial quality control in both the planning and execution of the paving plans and accurate survey measurements of the existing conditions. Weather played a significant factor in the schedule of this project. Although not necessarily delaying the paving schedule, there were months of weather-related delays in other areas. Higher than average winds, which prevented the barge from unloading materials and aggregates, plagued the first few months of the project. By executing an aggressive yet workable schedule, SWCP finished pouring concrete earlier than anticipated. This early completion was made possible by the quality control team and field superintendents' commitment to quality, ensuring only the highest quality PCCP was placed. The project was completed with 2-panel replacements out of over 100,000 square feet of PCCP. The Covid-19 pandemic began just before production was to start. The USAF personnel and leadership on the island worked with us to continue the project. SWCP was able to adjust the crew schedule and team rotations to provide such safe guards to prevent any out breaks of Covid on the island, keeping all personnel safe and maintaining the project schedule during a difficult and uncertain time.
Project Information:
Total Square Yards of Paving: 104,000 SY
Project Timeline: Novemeber 2019- December 2020
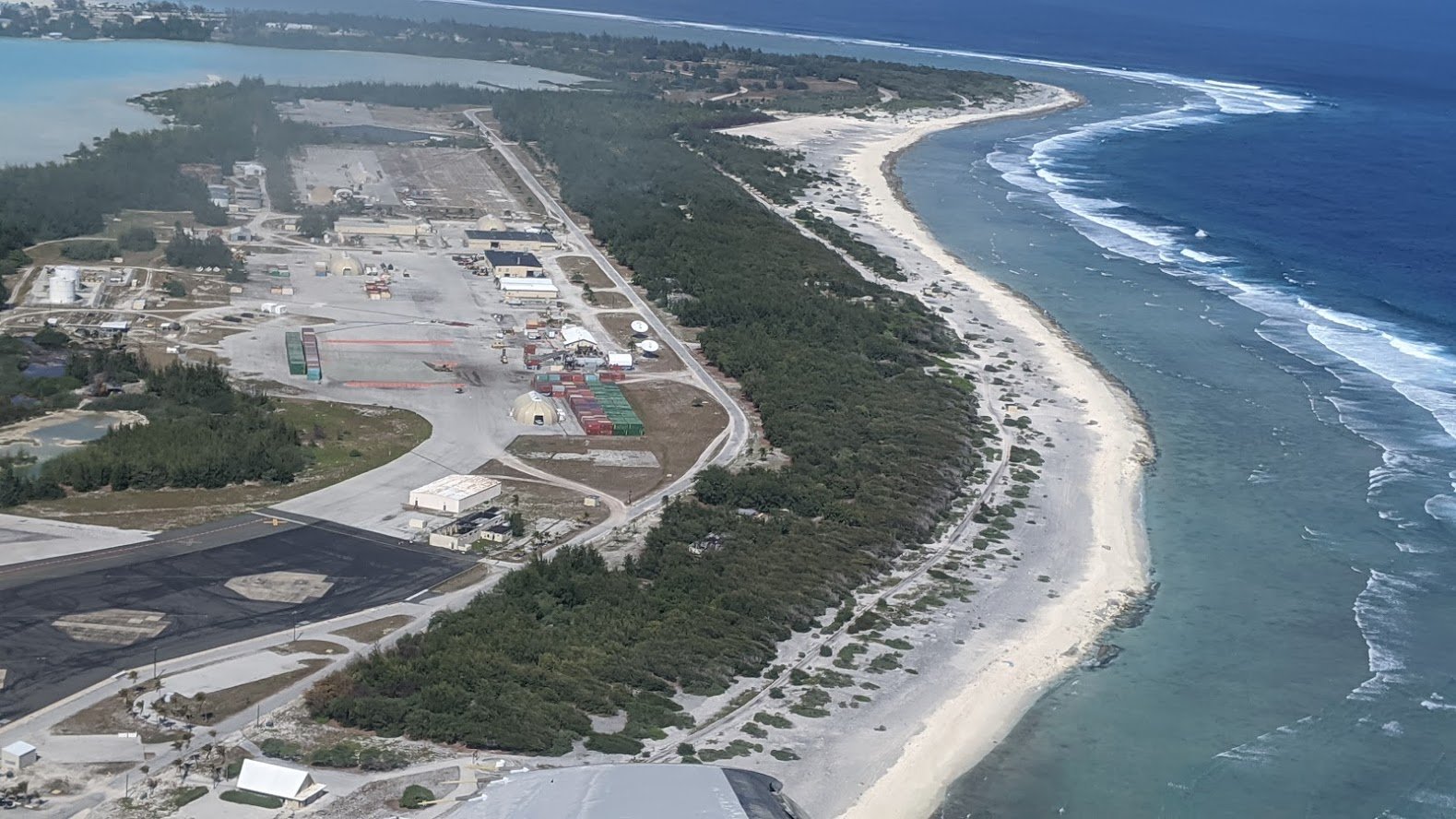

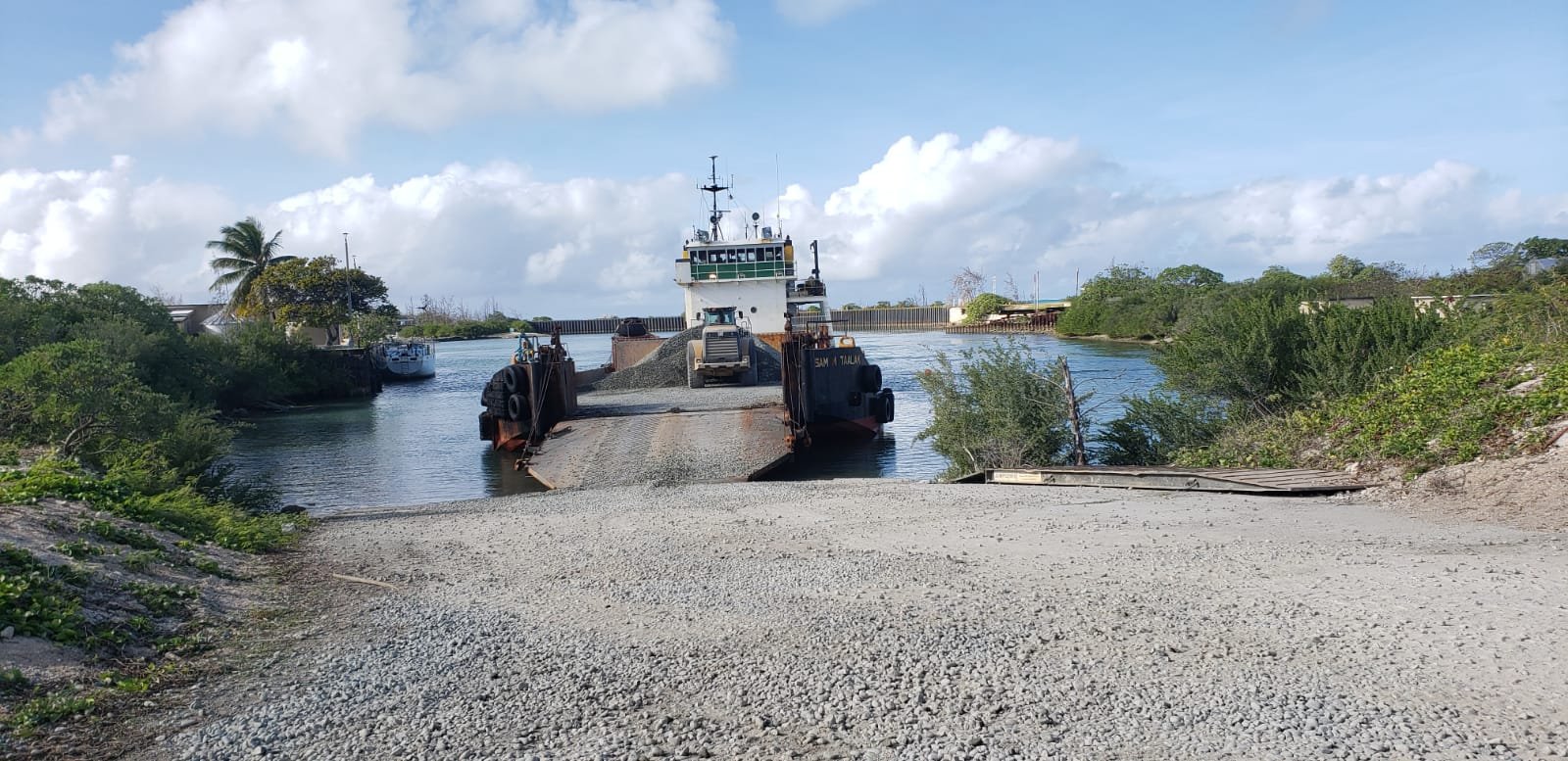
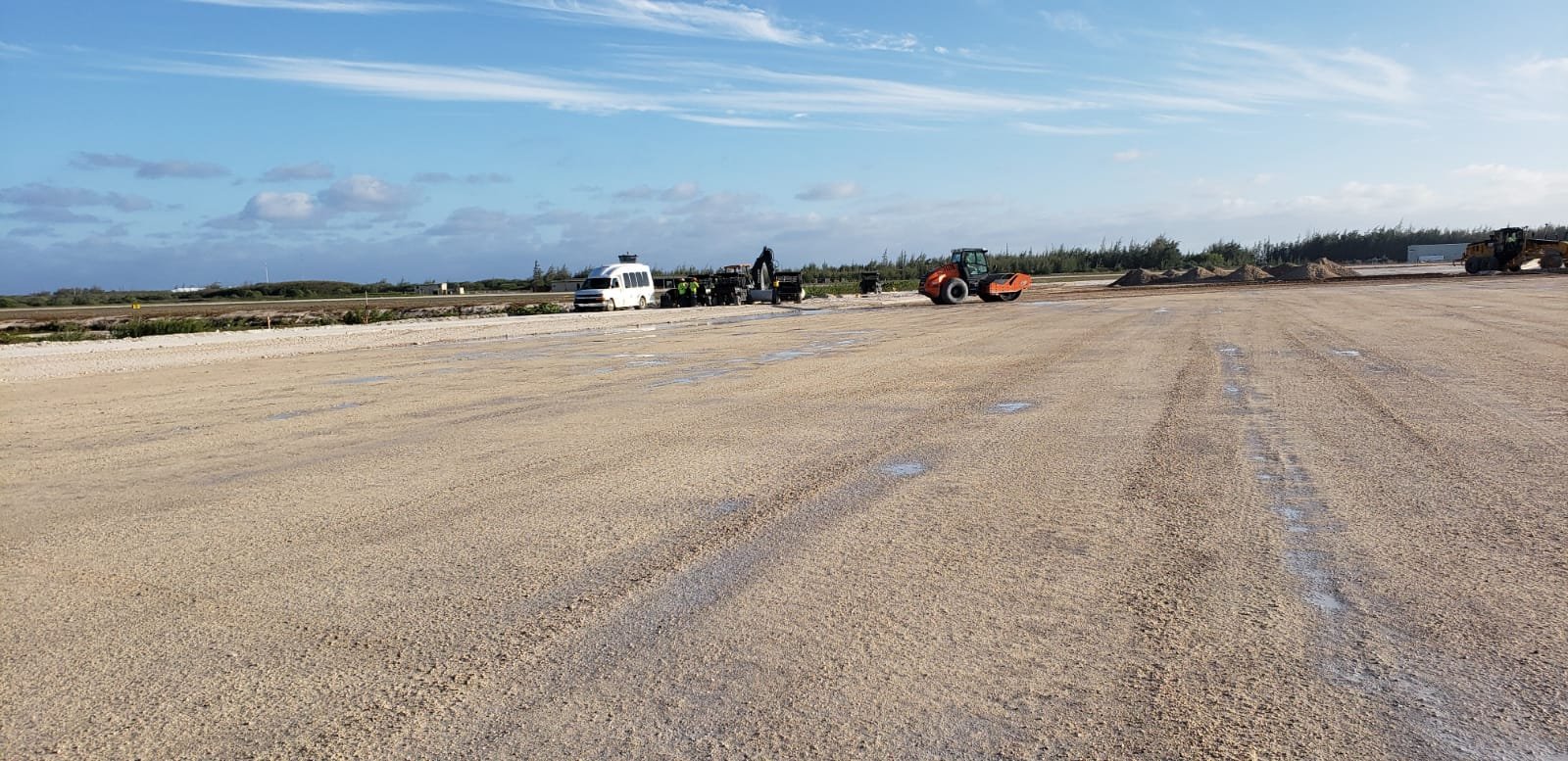
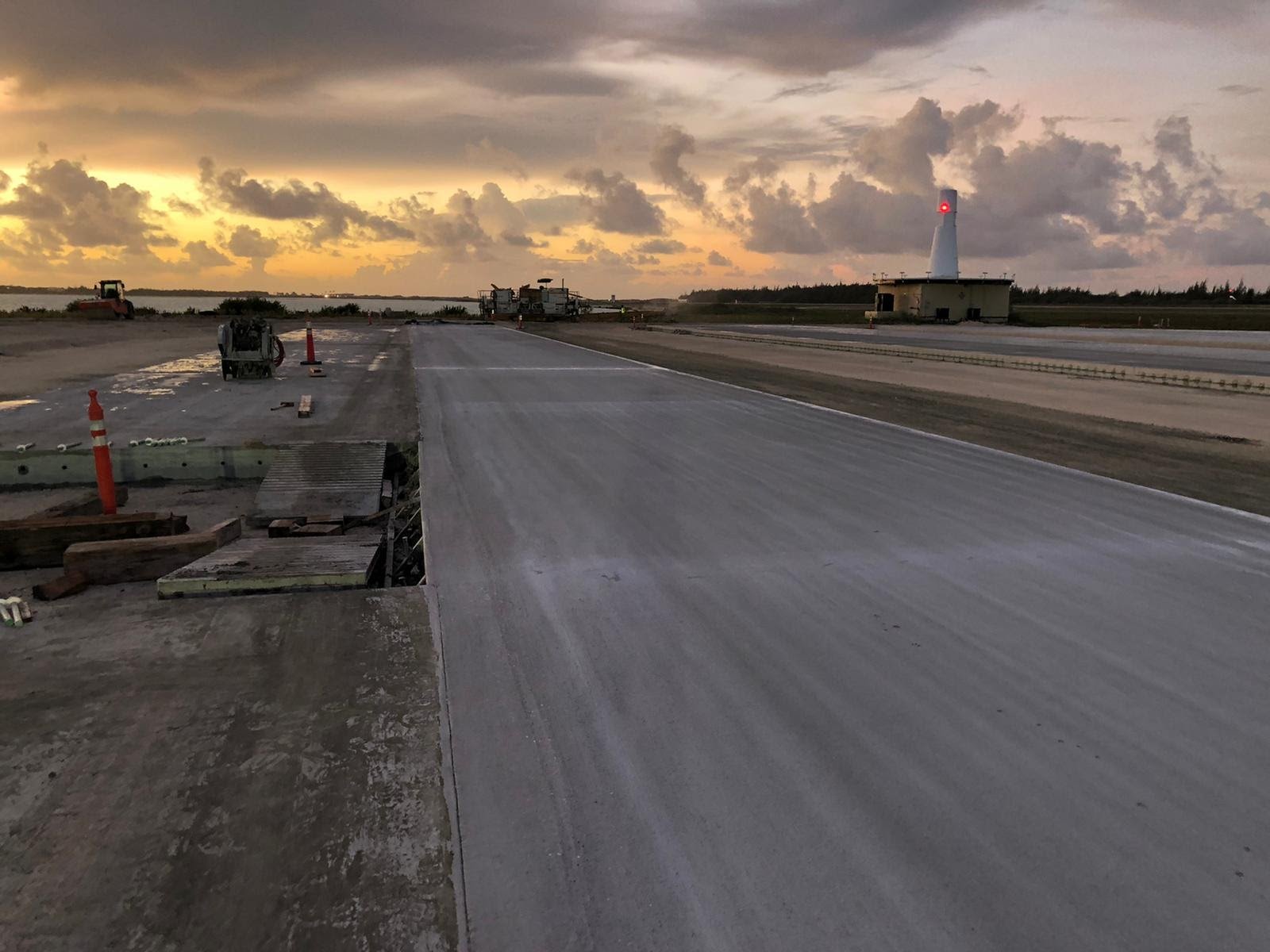
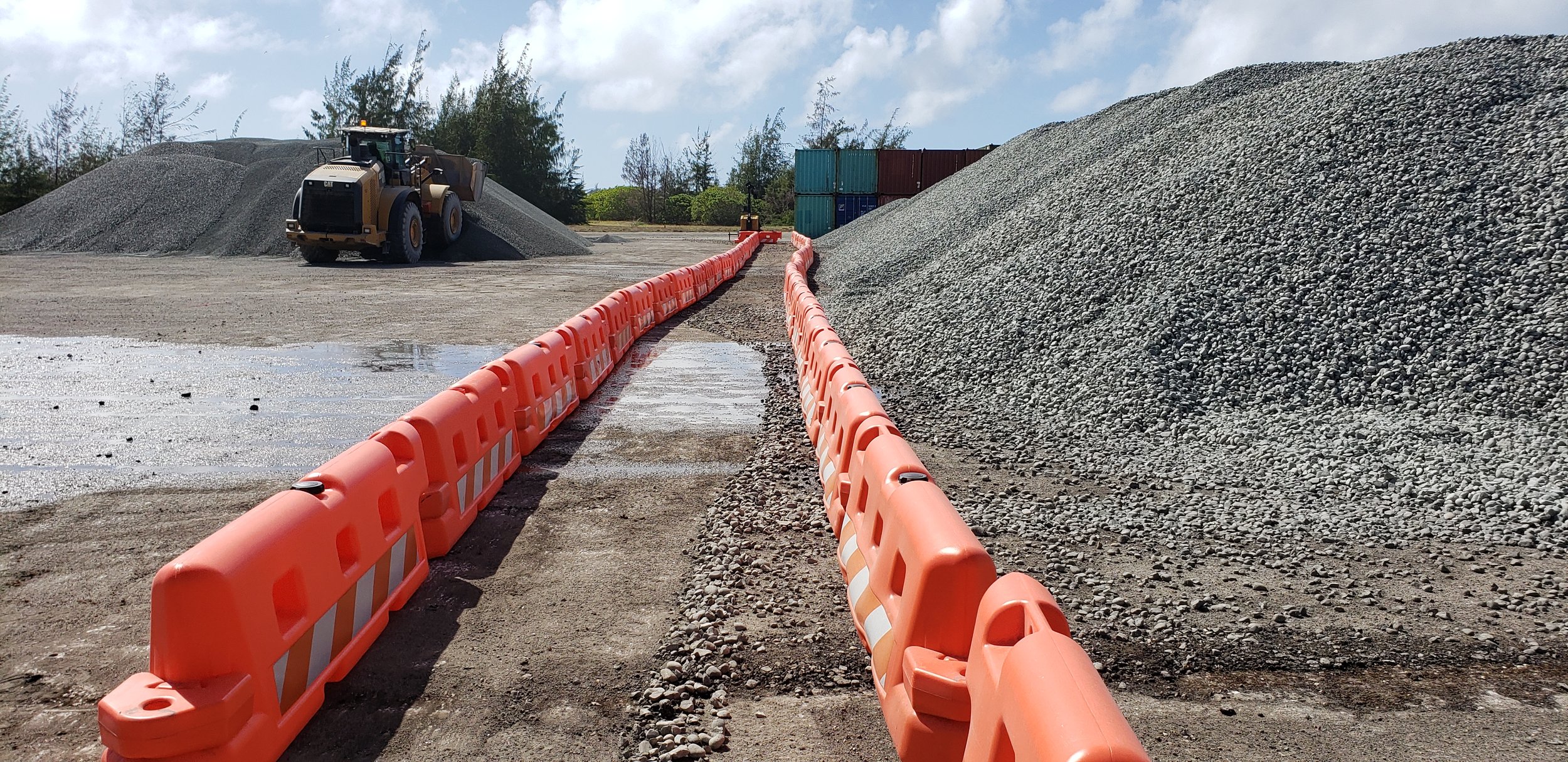
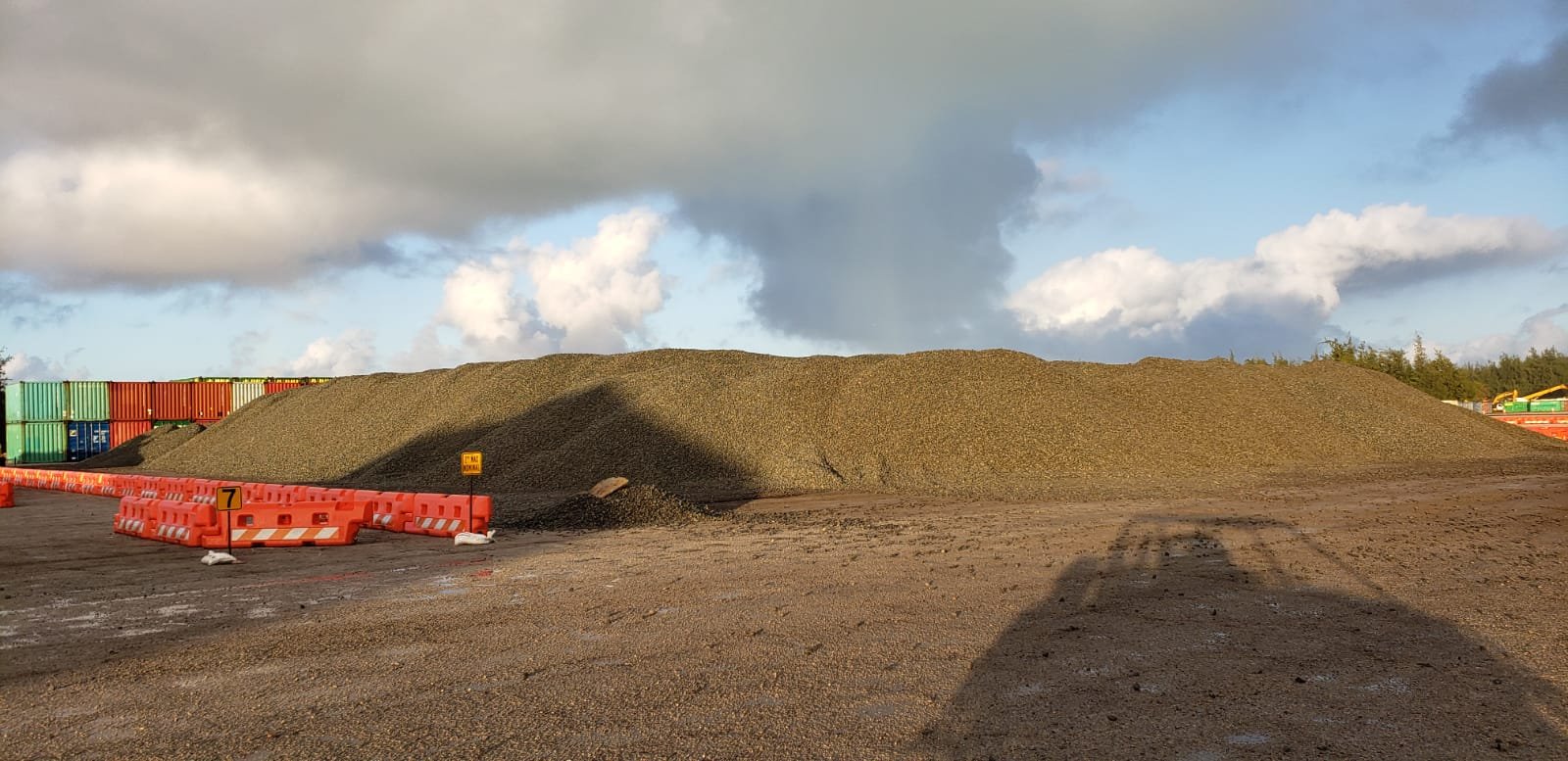
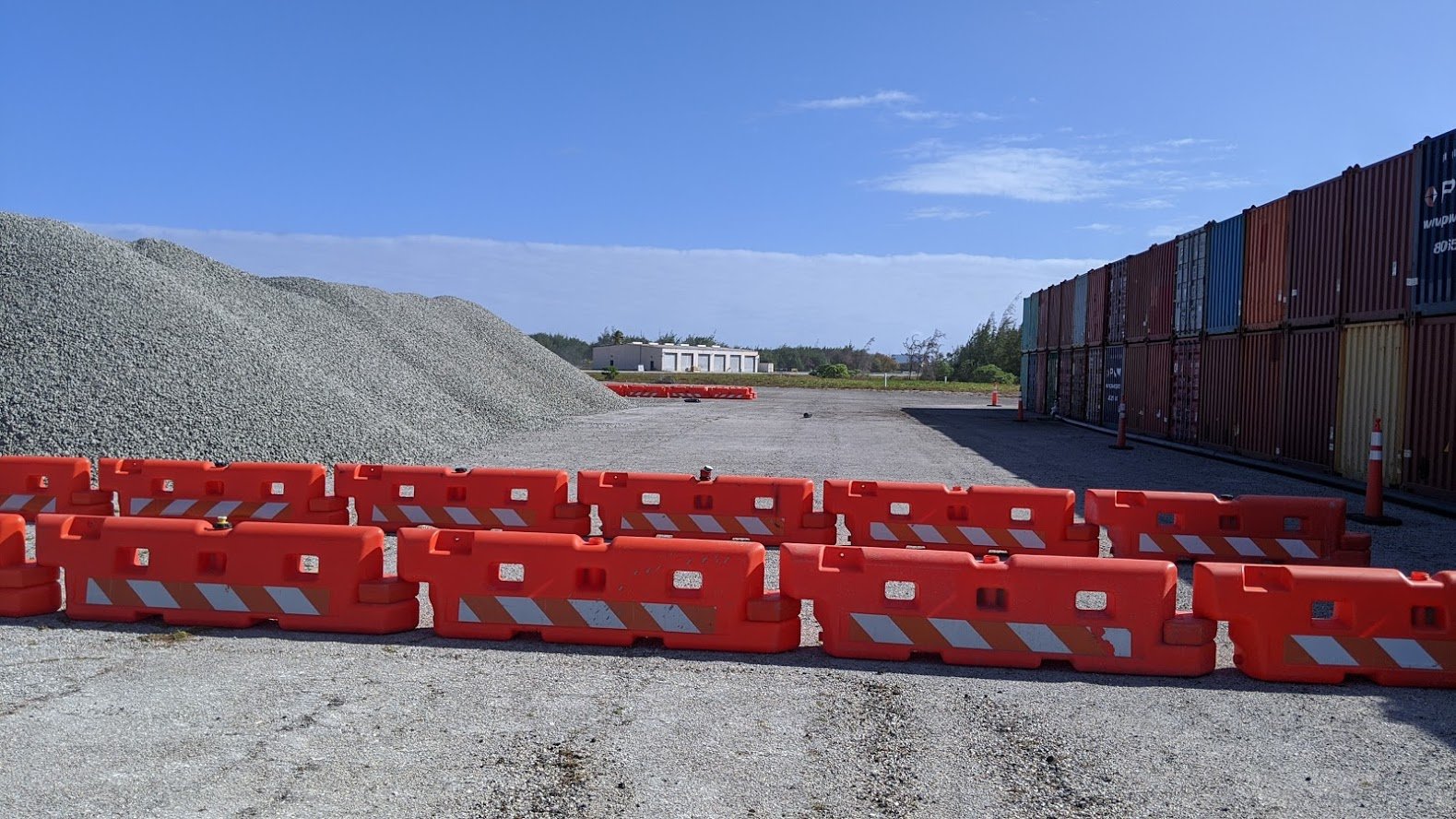
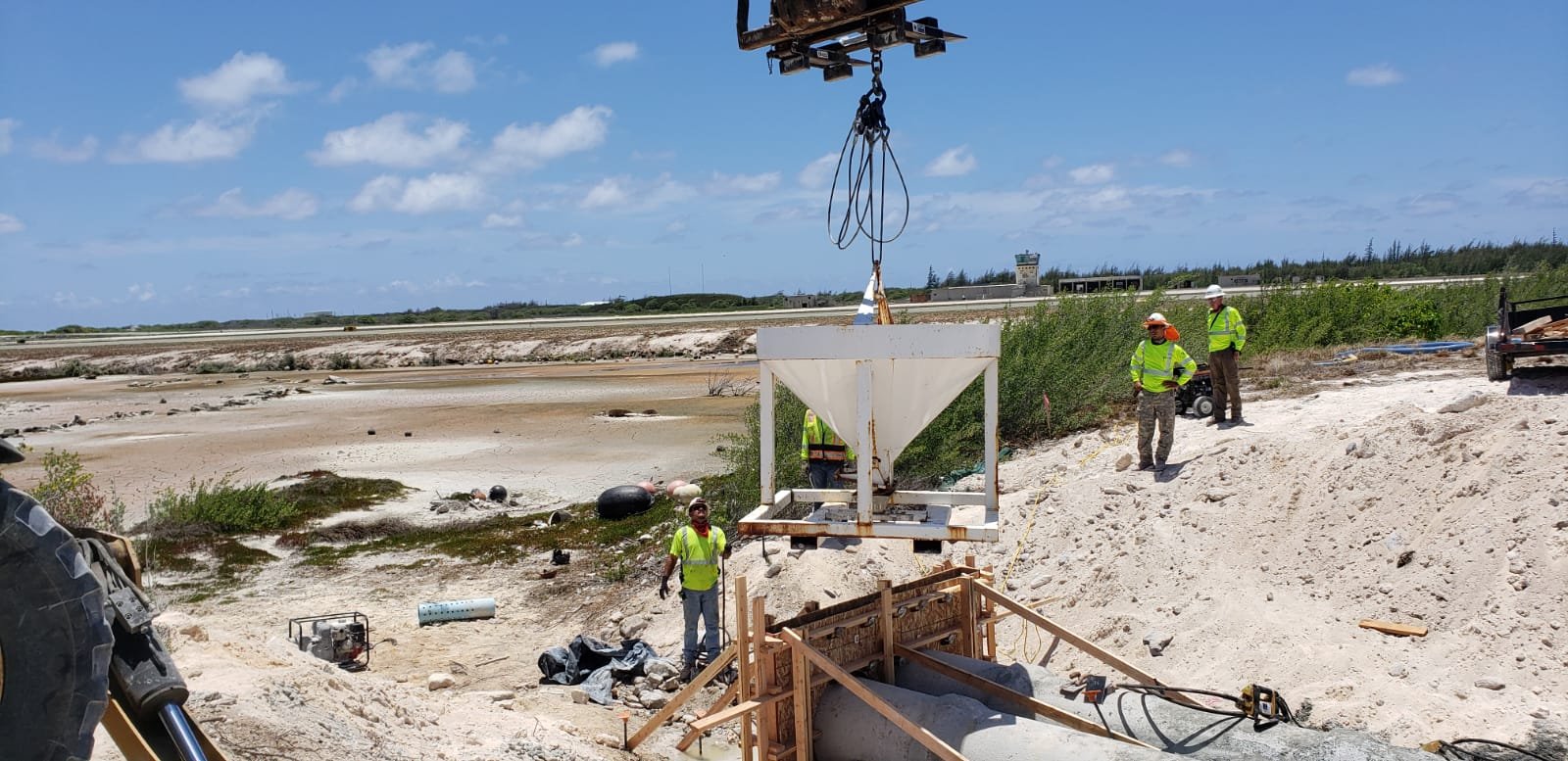
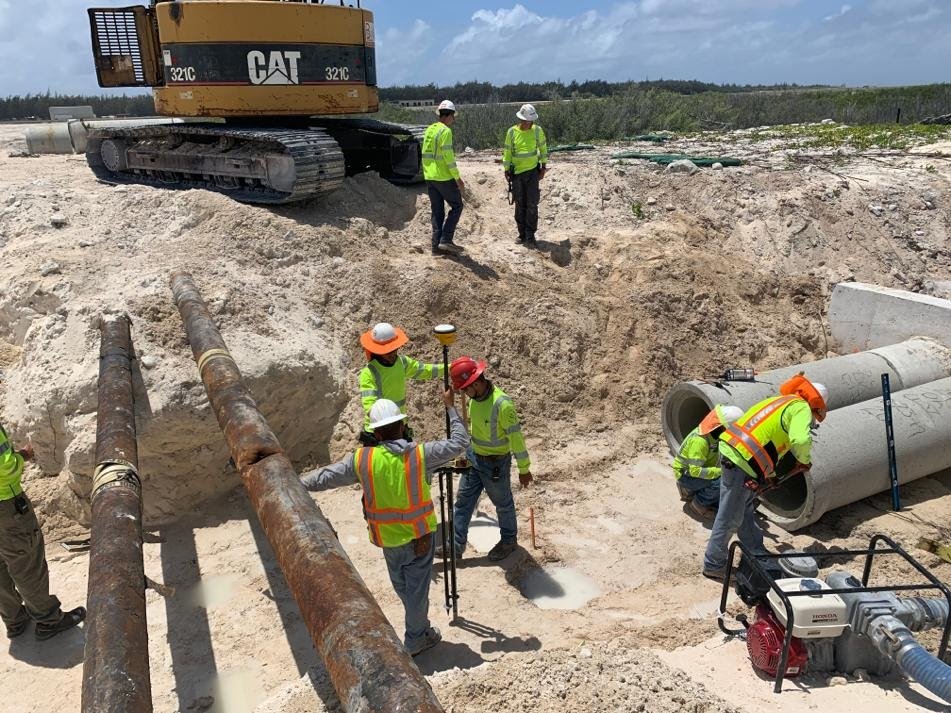
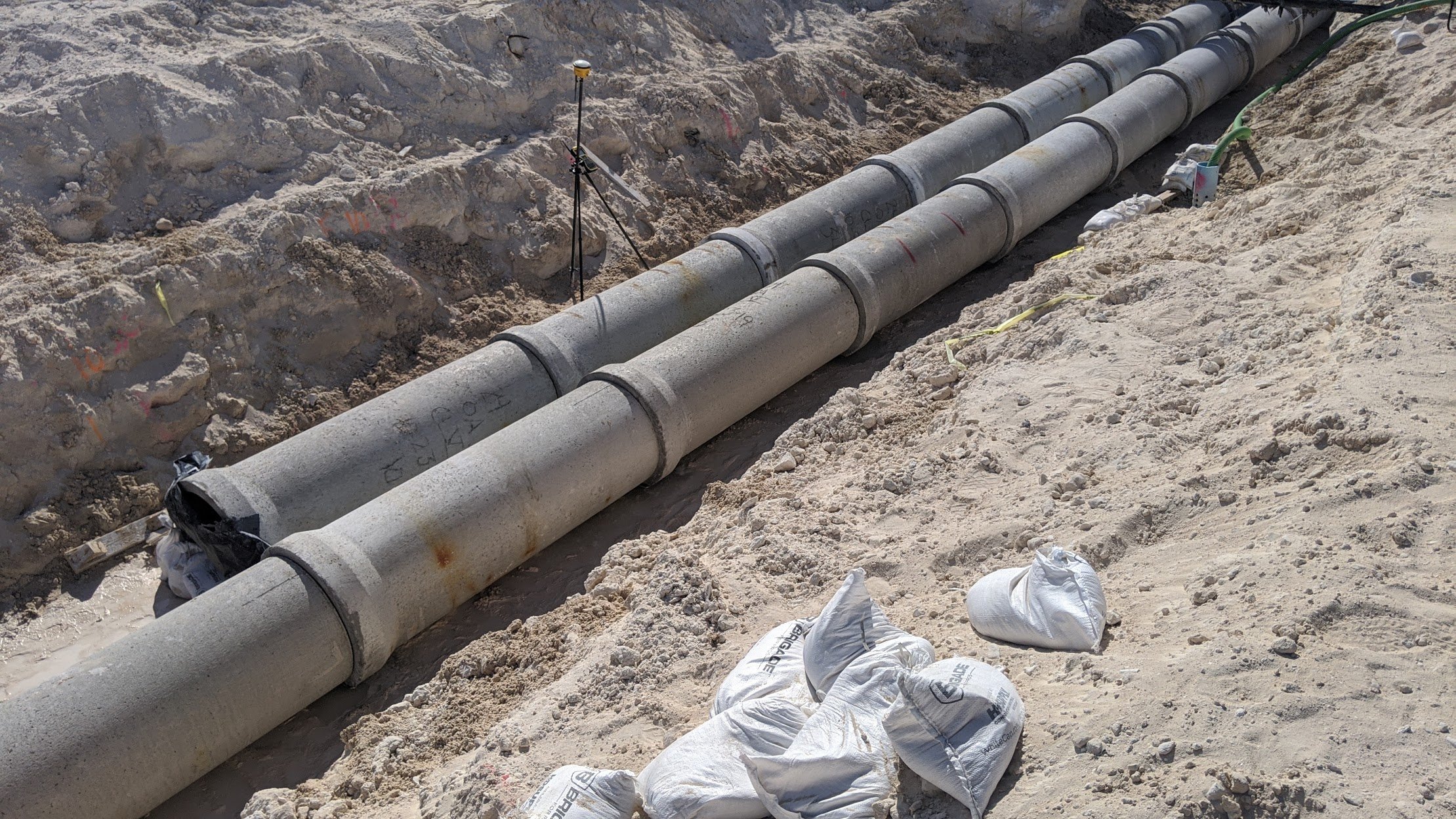
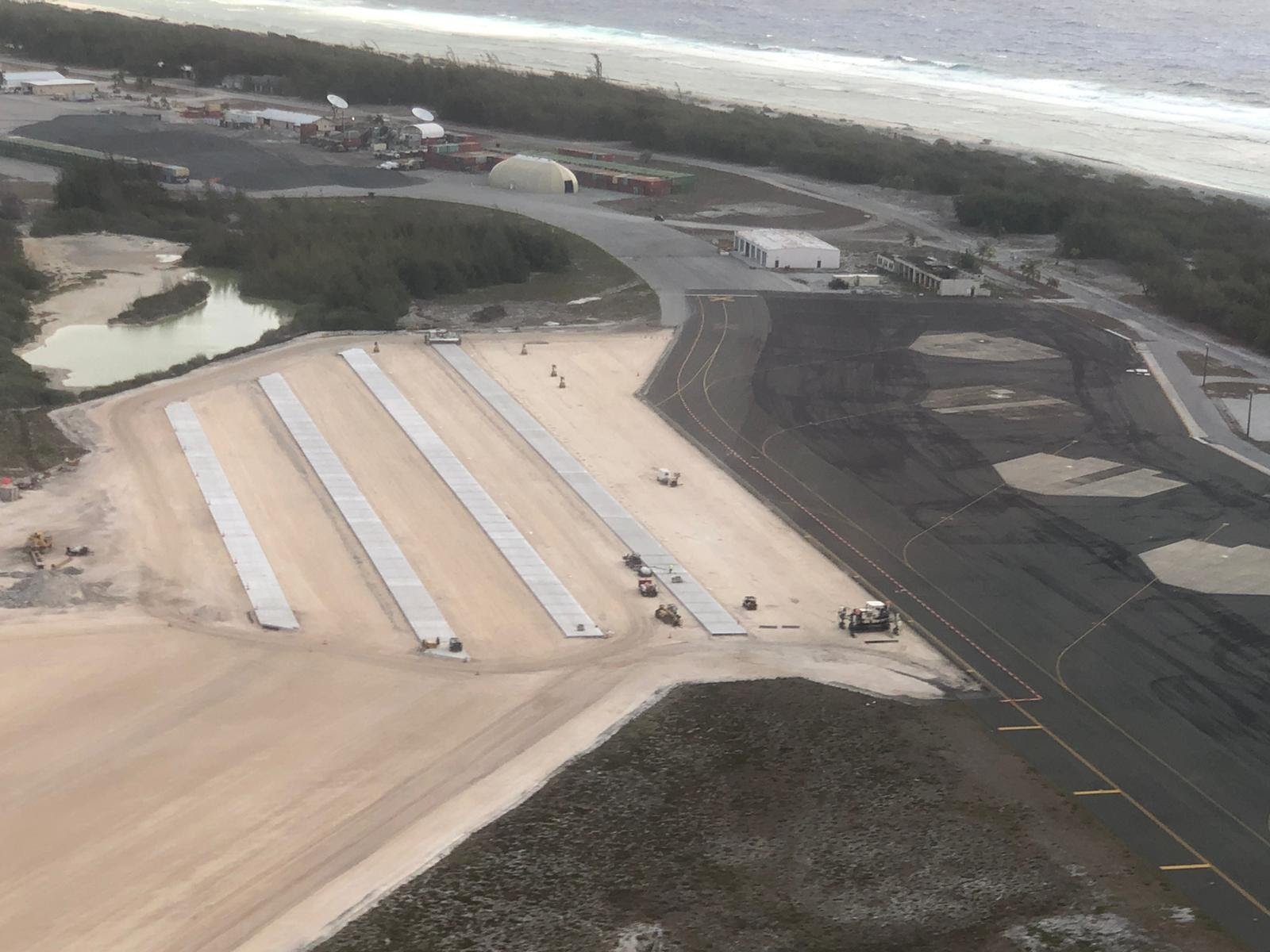
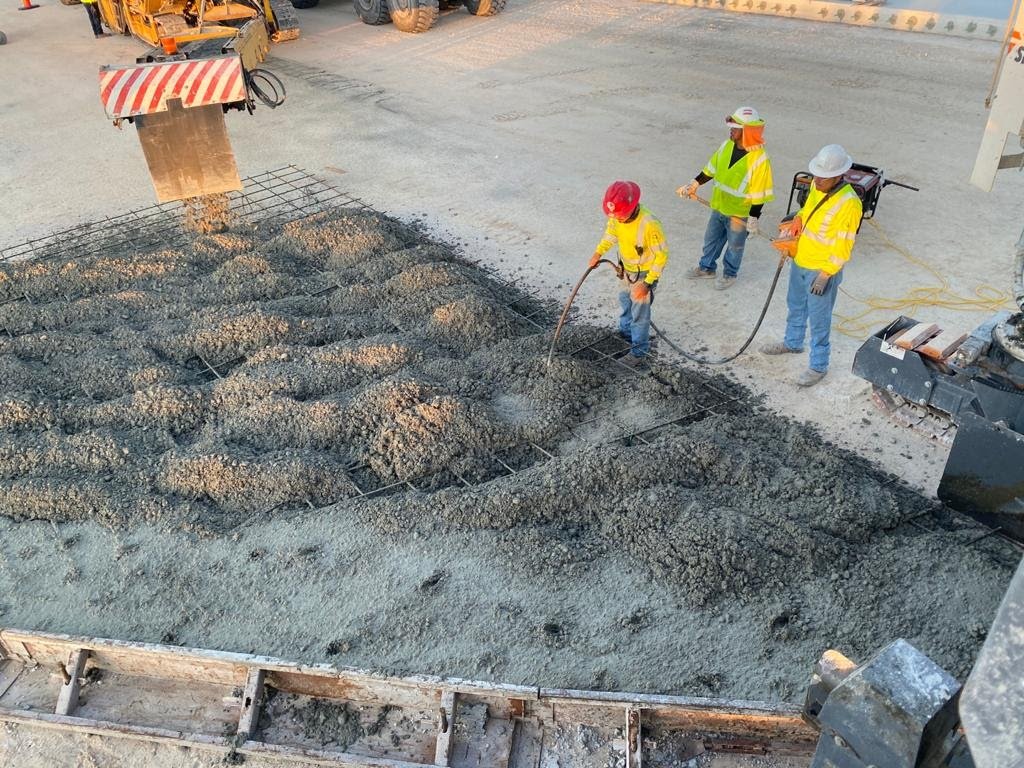
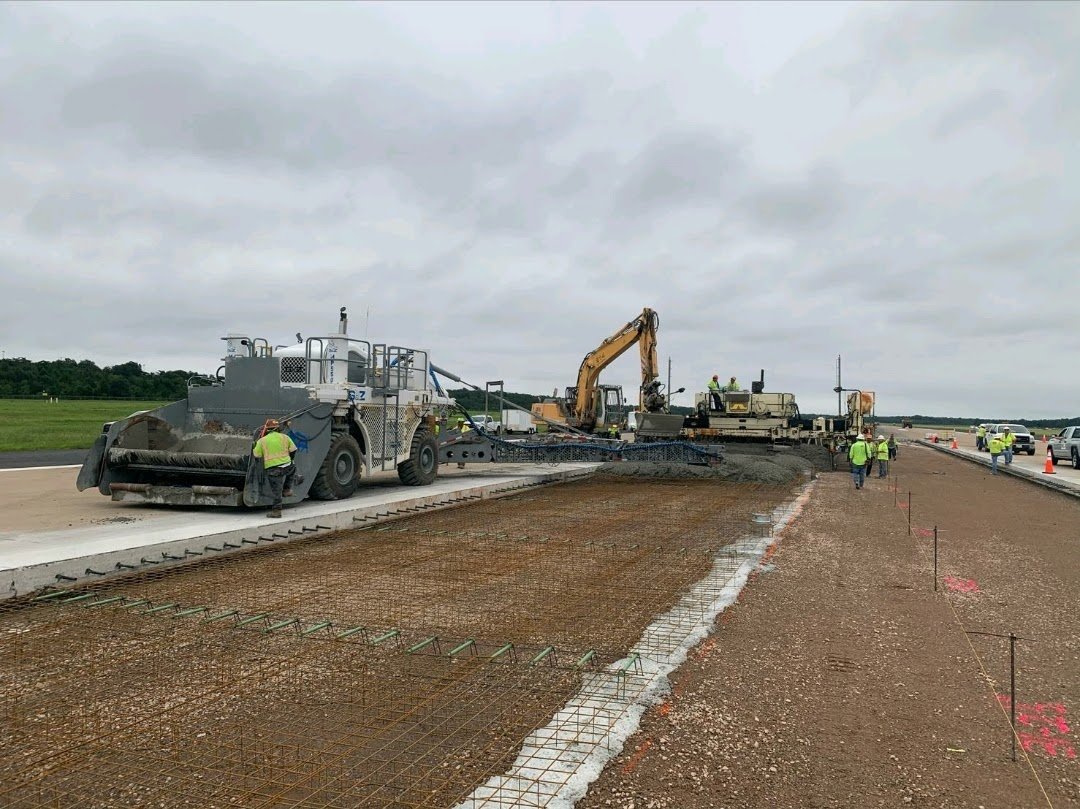
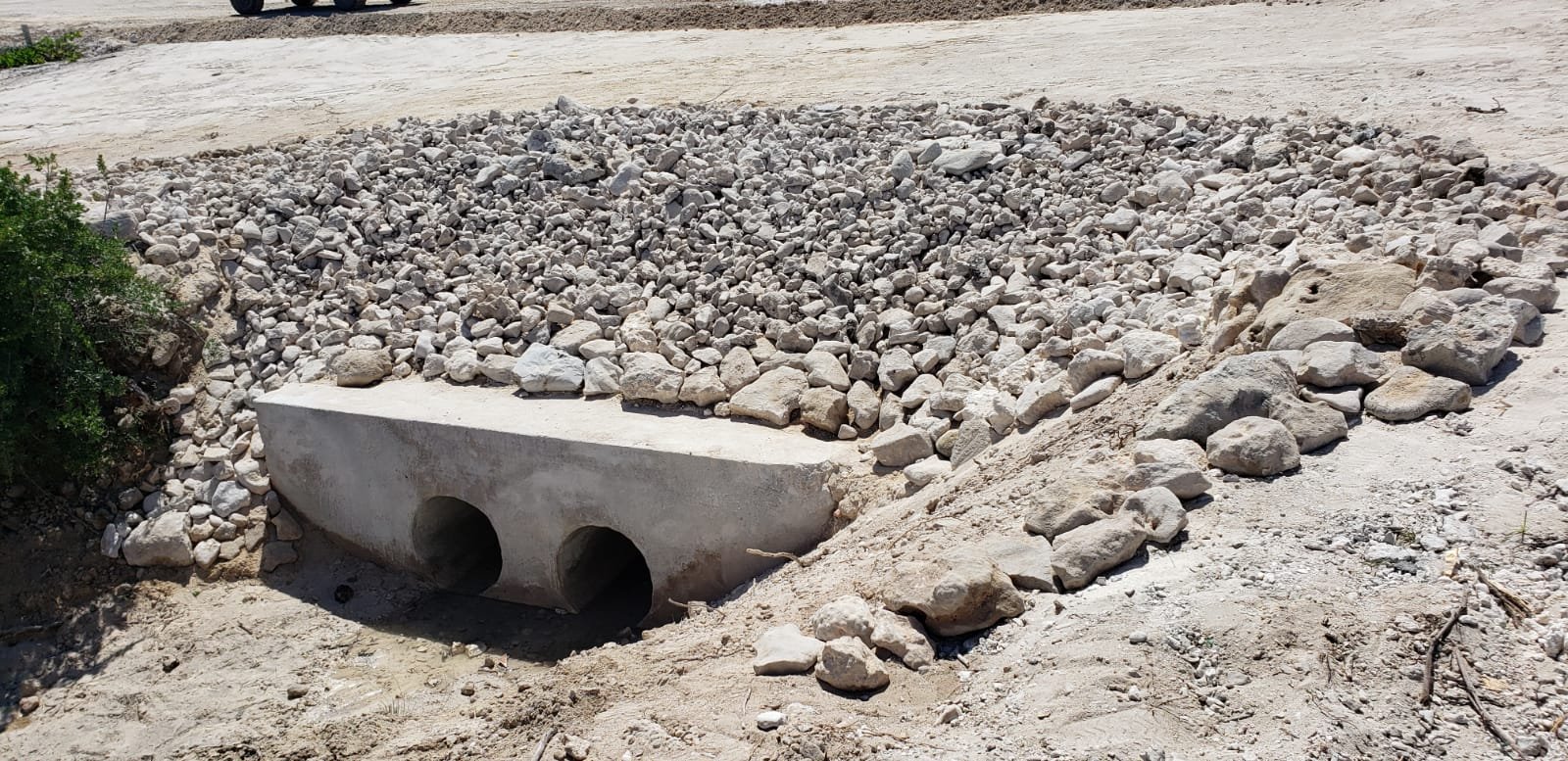
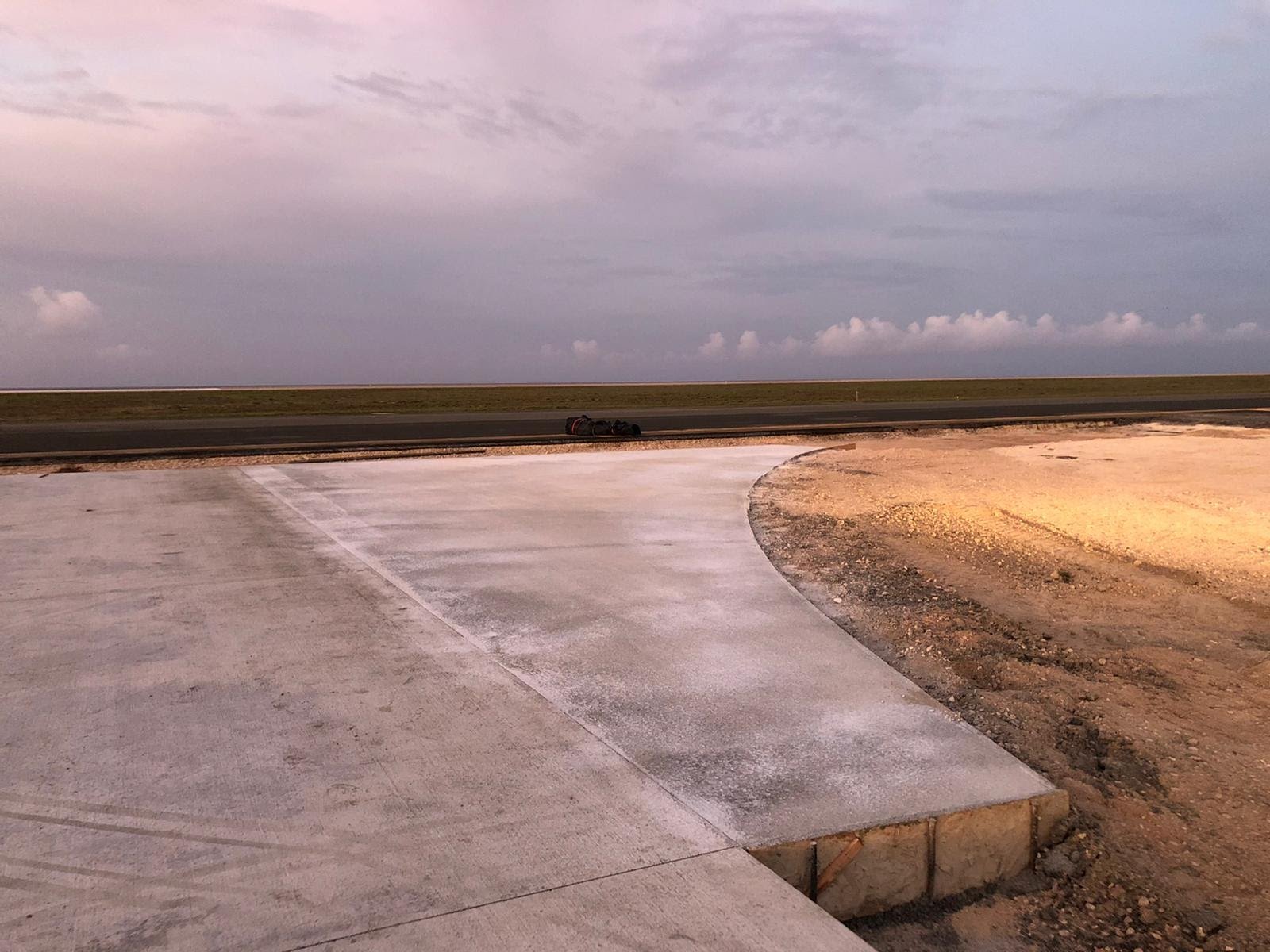
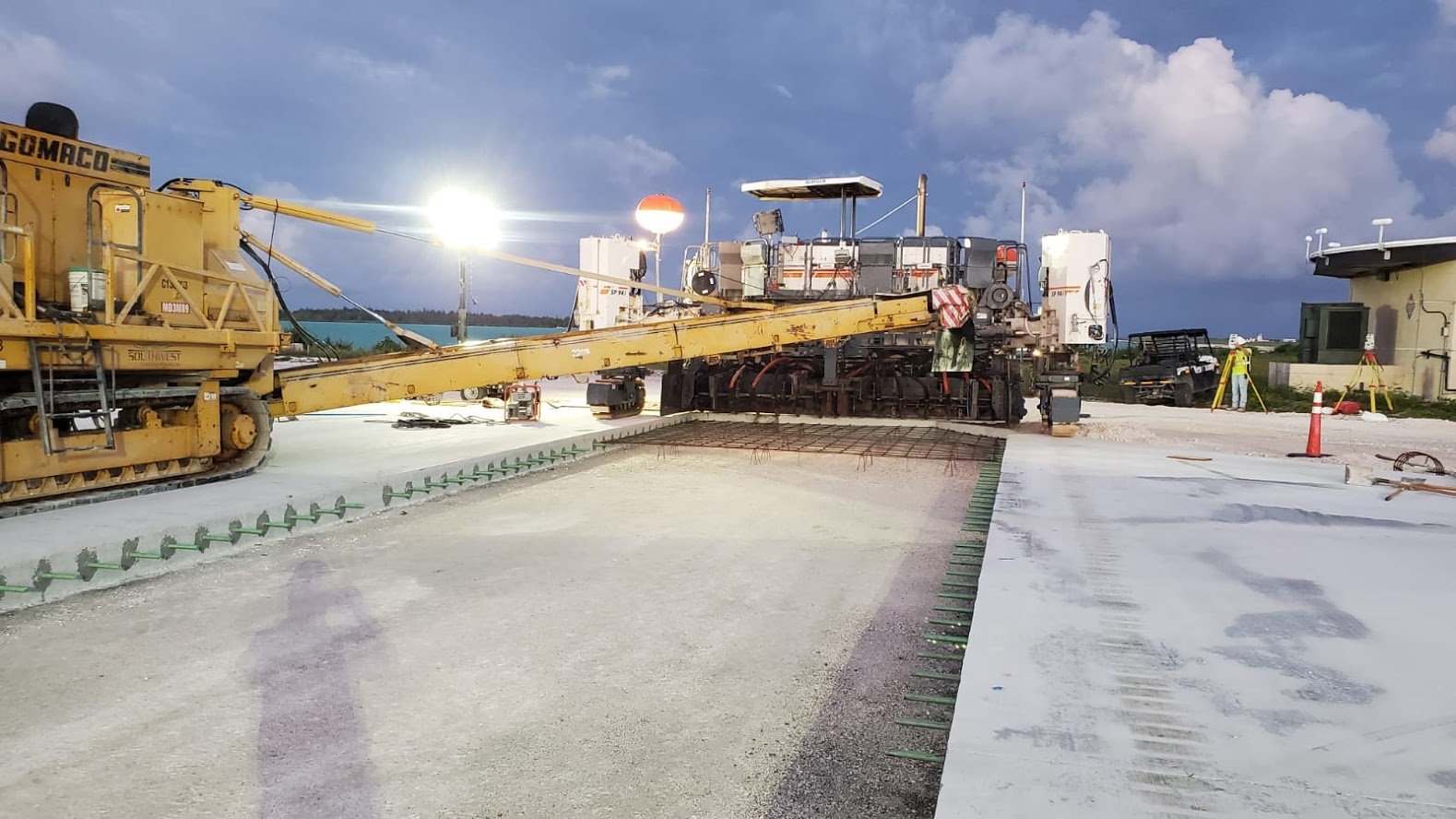
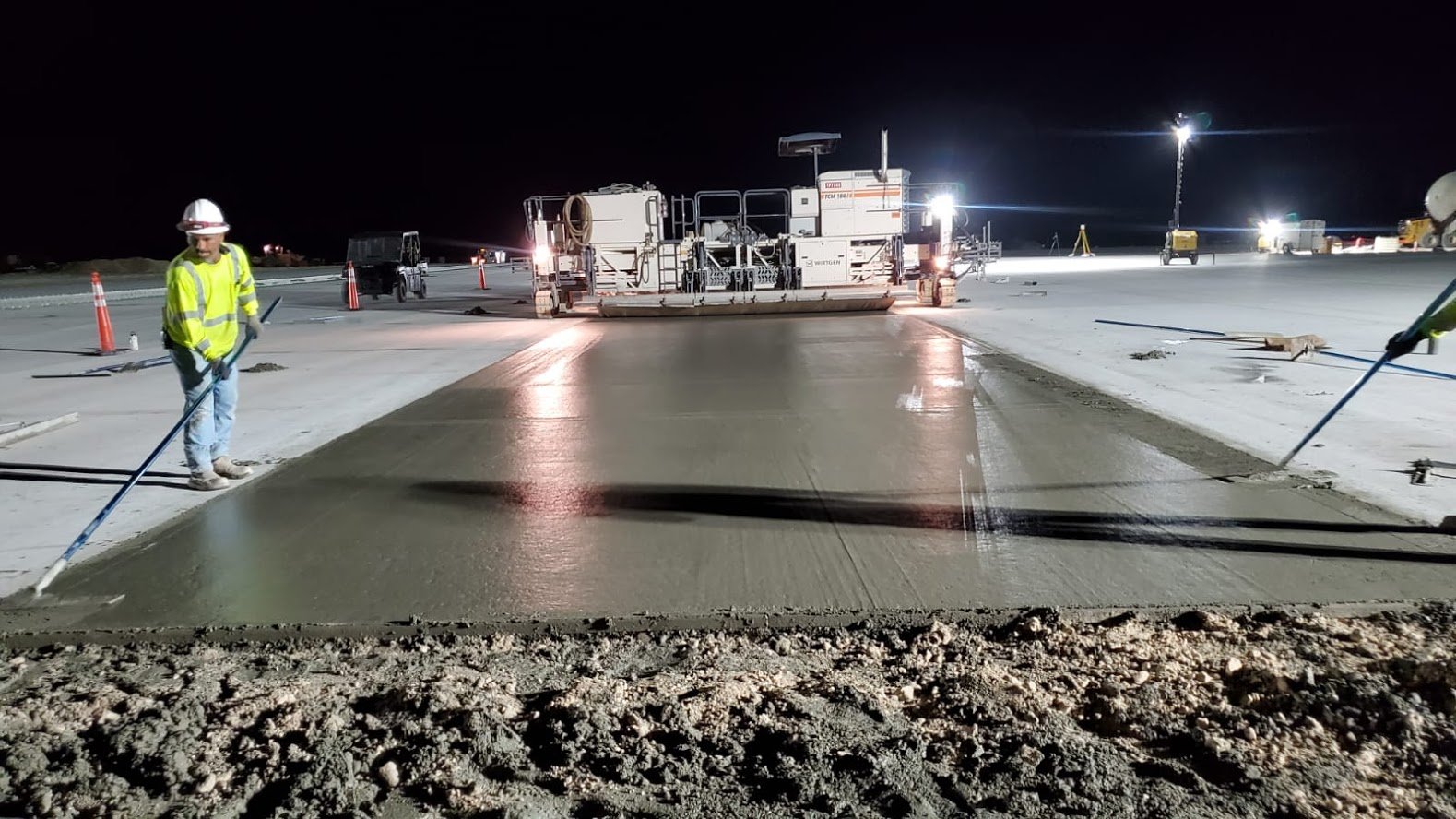
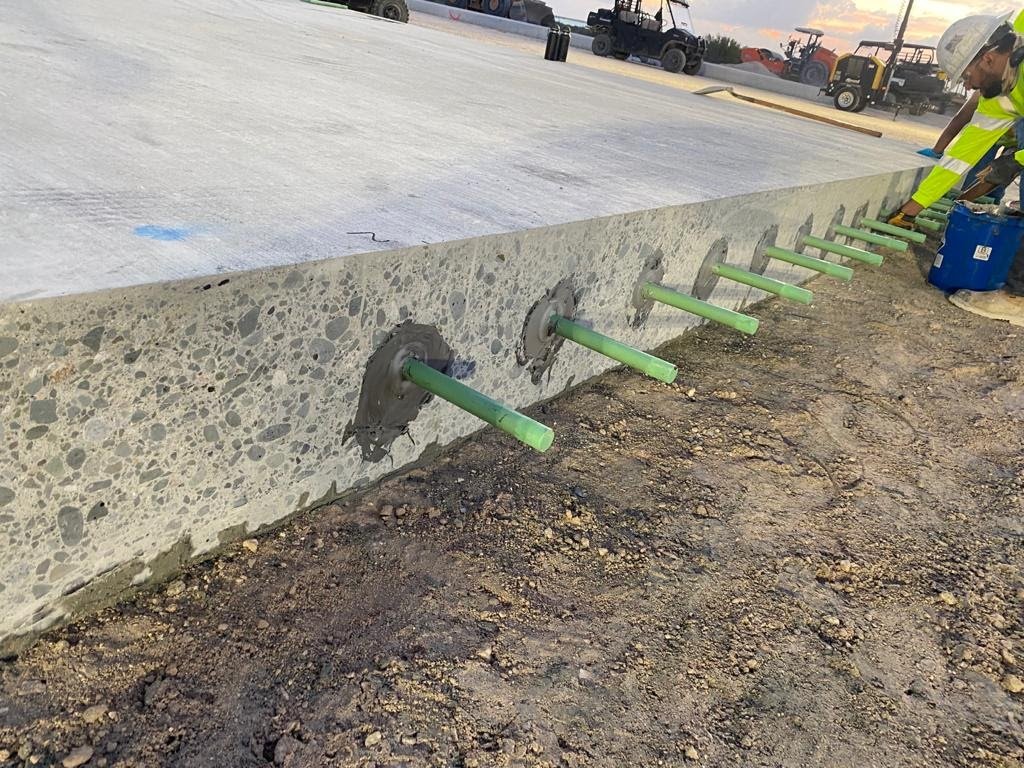
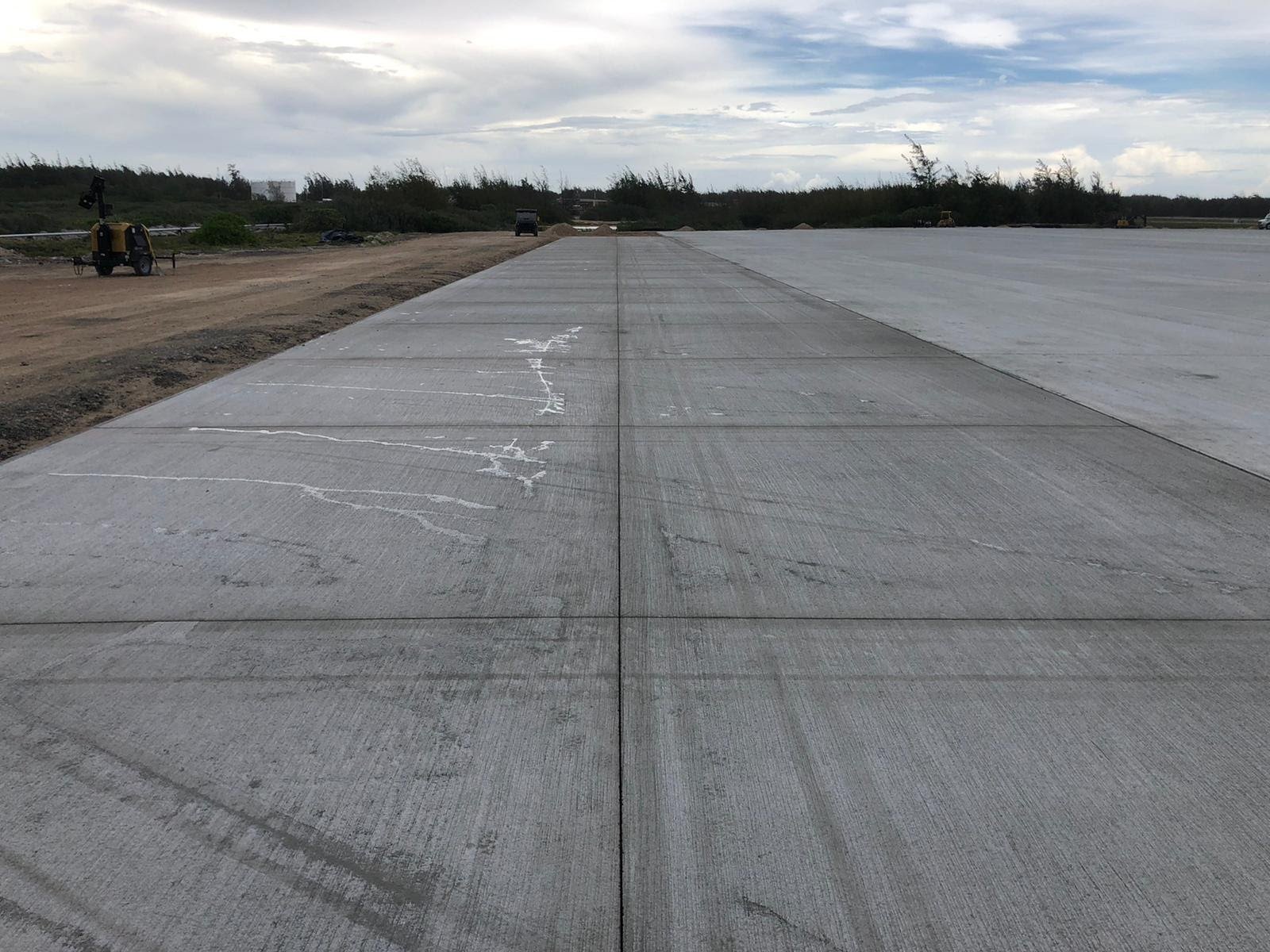
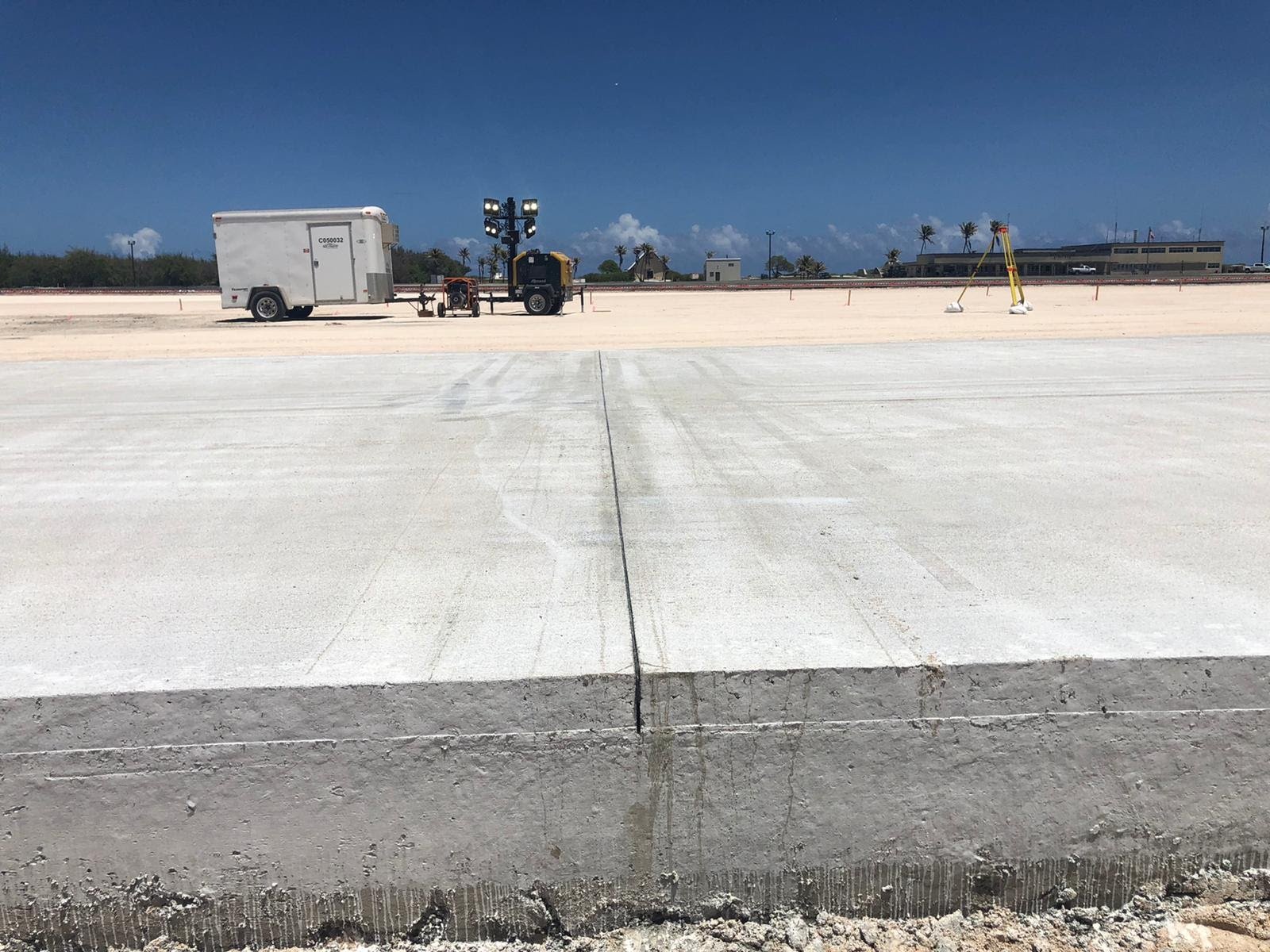
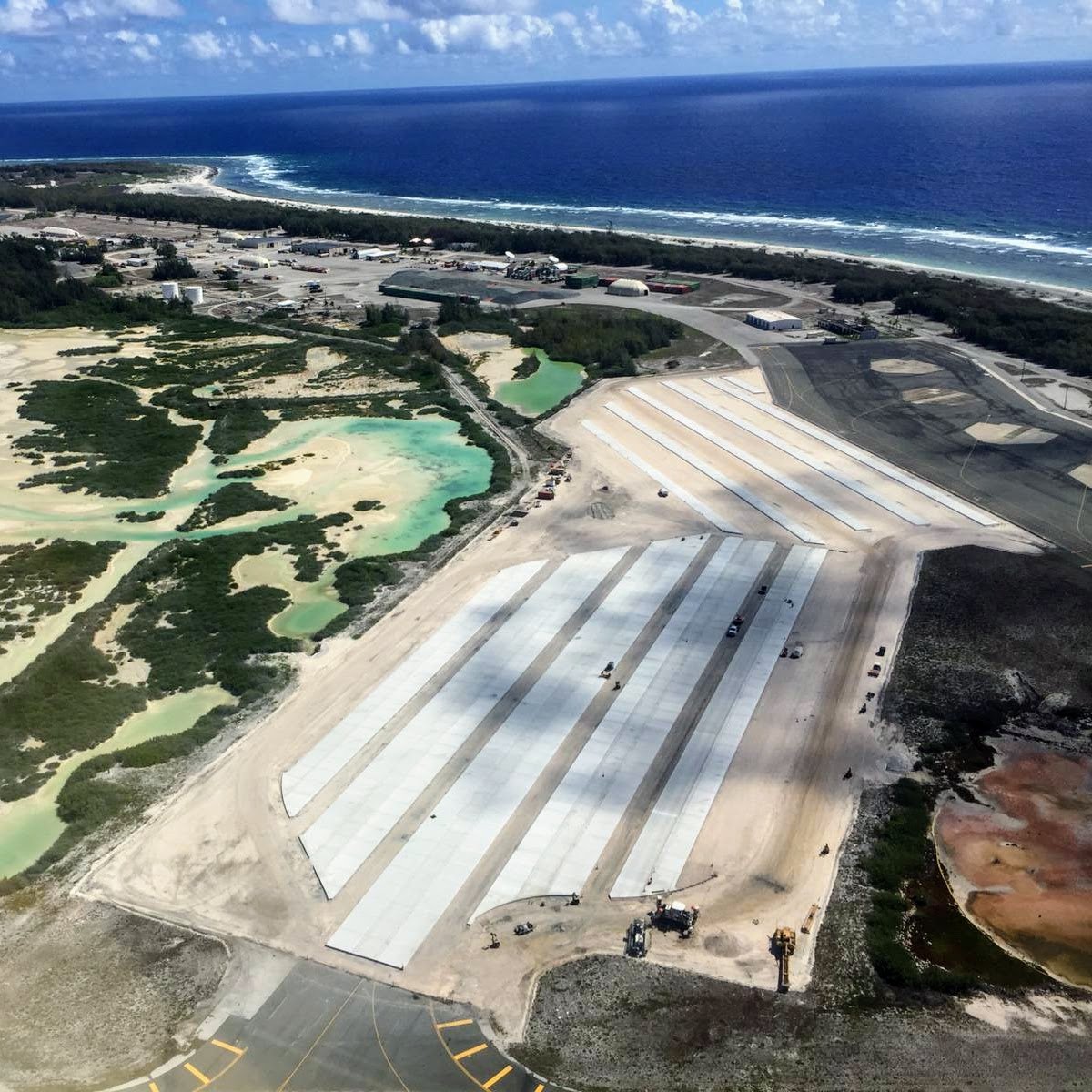
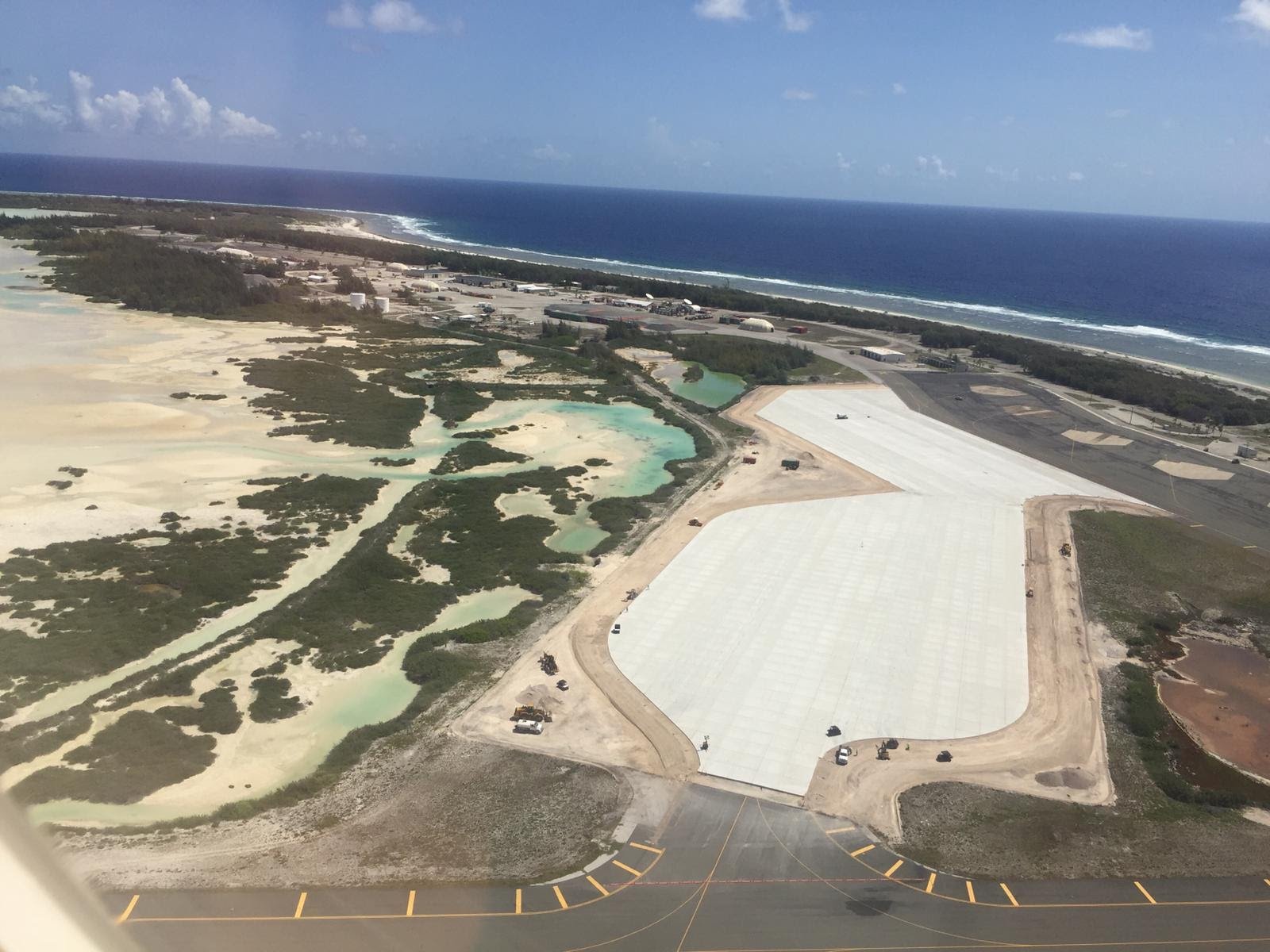
NAVFAC- P-284 F-35C Maintenance Hangar NAS Lemoore,CA
Project Summary
Southwest Concrete Paving (SWCP) served as a key subcontractor for the P-284 F-35C Maintenance Hangar construction project located at NAS Lemoore. The project consisted of a 110,793 SF Type I maintenance hangar; 900,800 SF of airfield pavement, including new taxiways tying into an existing apron, an existing taxiway tying into a runway, and a 3,670 SF munitions and storage facility; 28 new F-35 parking shade structures with electrical conduit and backerboards for each parking facility; 1,960 tie-down mooring points in the new apron to accommodate additional aircraft if needed; pavement markings; and a new subterranean stormwater retention system.
Paving for the project was done in two phases to maintain the schedule and accommodate the hangar construction. The first phase consisted of paving the main apron, two new taxiways, a liquid oxygen storage facility pad, a wash rack, and storage facility access. Paving lanes measuring 37.5 feet in width were placed using a Gomaco GP 4000 paver with an automated float for finishing and Gomaco TC 600 texture cure machine for burlap drag and cure application. The second phase was completed after the hangar had been completed, allowing the main apron to be protected and not utilized for hangar construction access and staging. This phase consisted of two hand pours that tied the main apron to the hangar floor. Typical joints for both phases were undowelled contraction joints except for the south and east edge having three rows and two rows respectively of dowelled contraction joints. All construction joints were dowelled using 1.25" x 20" epoxy-coated dowels. All dowels at construction joints were installed using a drill and epoxy method utilizing a three-gang Minich drill.
Bulk delivery of aggregates to support paving was challenging due to the location of the airfield side of the air station; trucking access was severely restricted. Delivery vehicles traversed two separate inspection stations, frequently having significant wait times. SWCP worked with its prime contractor to circumvent this issue by creating an enclave around the project site and enabling farm roads on the back side of the air base for delivery vehicle access. This approach significantly reduced the time trucking vendors were stuck in inspection lines and greatly simplified material delivery for phase one of the project, although phase two required traditional site access through the inspection gates.
The project had more than 1,900 tie-downs installed in the plastic concrete, plus 28 parking stalls, all with electrical stubs through the pavement. Despite a myriad of obstacles throughout the pavement section, SWCP achieved consistently low profiles and met all straightedge and finished grade elevation requirements in the UFGS 32 13 14.13 specifications. SWCP received 100% pay with zero grinds on the entire project.
Project Information
Project Timeline: 3/2018-3/2022
Paving Length: 92,896 SY
Total Square Yards of Paving: 100,089 SY
Total Lane Miles: 3.9 Miles
USAF- CTF Compound Renovation- Edwards AFB, California
Project Summary
Southwest Concrete Paving (SWCP) served as a key subcontractor for the Combined Test Force Compound Renovation project at Edwards Air Force Base in Mojave, California. The project involved renovating all four hangars located in a hangar complex with a parking and access apron. This design-build project with Harper Construction (Harper) included structural repair work to the buildings by Harper and removing and replacing the primary apron, five ancillary access aprons, and a taxiway by SWCP. The new section consisted of more than 87,000 SY of pavement and aggregate base. Paving Concrete paving for the project consisted of placing 14-inch-thick airfield concrete utilizing UFGS criteria in section 32 13 11. Due to existing drainage conditions, design grades on the primary apron were extreme. Several grade breaks in the apron were unpaveable, requiring hand work to meet design grade criteria. The primary lane width was 20’ feet. However, there were multiple joint width adjustments, and the five support aprons located directly adjacent to and next to the hangar buildings had several different joint patterns. Due to the width changes that were required for the project, SWCP mobilized two pavers to facilitate the construction of the various sections without requiring recurring width changes. The primary paving on the main apron was constructed with a Gomaco GP 4000 paver. Once the main apron was completed, the GP 4000 was resized and utilized to construct several of the support aprons. A Wirtgen SP i94 paver was mobilized to the site to help accommodate odd paving widths and was used in tandem with the GP 4000 to construct the ancillary apron work on the project. Joint spacing was variable throughout the job, and survey was critical to identify proper joint alignment and allow the pilot and fill lane transverse joints to match.
On-Site Batch Plant
An on-site batch plant was mobilized and erected at the job site. While project specifications required an on-site plant, the plan sheets did not identify a location, so the placement of the plant was negotiated with the base. The parking lot behind the hangar buildings was the agreed-upon plant location. This area provided an asphalt surface ideal for aggregate storage. However, existing light poles throughout the lot hindered main plant placement and created obstacles for trucking during wet haul and aggregate and cementitious delivery. Other modifications to the lot included constructing a pad for the main plant to sit and bringing electrical to the site. Ultimately, the plant was wedged in and supported paving operations nicely. Its location, immediately behind the hangar buildings where concrete was being placed, helped minimize delivery times, which became a critical feature in hot weather paving. Air quality permitting of the plant became a secondary challenge once a location was chosen. With the plant in Kern County, SWCP was required to obtain separate permits and inspections from state and county air quality agencies.
Recycling
A significant challenge that had been a concern since bidding the project was the off-haul of the demolished concrete. Edwards AFB is located in a remote part of the Mojave Desert, and the CTF compound is situated well within the heart of the base, whose gates stretch for many miles across the sprawling desert and surrounding dry lake beds. Removal of the demolished concrete was a trucking and logistical concern from day one. SWCP proposed a value engineering (VE) modification to the Government to recycle the demolished airfield concrete and utilize it for the subbase on the new section. The Department of Defence (DOD) has previously used recycled concrete as bases and subbases. However, several of those projects had turned out poorly due to what had been determined to be ASR and sulfate reactions propagated from using recycled concrete. The DOD had researched the risk and had an in-place Engineering Technical Letter (ETL) regarding using recycled material in airfield paving. Fortunately for SWCP, the technical team assigned to the project was strong, and SWCP walked through the testing and evaluation process with the on-site team to quantify the risk based on the mitigation outline provided in the ETL. During the discovery phase, it was determined that the risk of both ASR and sulfate attack from concrete recycling was low, and the Government ultimately approved the VE. Once approved, SWCP mobilized a track crusher to the site and successfully demolished, crushed and recycled the existing pavement, placing the new material at 95% compaction of modified effort (ASTM D1557).
Hot Weather Paving
As a subcontractor to Harper Construction on the project, SWCP did not control the scheduling of the phasing. To that end, the job was prepared for SWCP to begin concrete paving in early July – at the height of the hot, dry Mojave Desert summer. To mitigate the dry conditions, SWCP employed several methods. First, the batch plant mobilized a 25,000-gallon tank and chiller to cool batching water. Feed water was cooled in the chiller tank and maintained at around 40°F during the hot weather activities. At the aggregate stockpiles, a series of high-pressure water sprinklers were installed around the area. Winds in the desert typically kicked up in the afternoon and were frequently over 20 mph. While not ideal for paving, SWCP utilized this as a cooling method by wetting the aggregate piles in the afternoon and creating evaporative cooling on the material, which increased as the overhead sun began to dip on the horizon. Typically, winds began to subside shortly after sunset, around 9 or 10 pm, and conditions were as benign as possible. SWCP capitalized on the best-case weather window and began shifts during this timeframe, paving into the following morning past sun-up. In addition to scheduling and mix cooling efforts, SWCP employed a Boss-Tek fogger during all hot weather paving operations at the paving site. The fogger was utilized to increase localized humidity above the fresh slab behind the paver and minimize moisture loss in the aggregate base and slump loss of the placed concrete head in front of the paver. These mitigation measures worked well in tandem, and SWCP had zero plastic shrinkage cracking observed on the project.
Project Information
Timeline: 01/2018- 03/2019
Total Square Yards of Paving: 87,033 SY
Total Lane Miles: 7.54 Miles.
Number of Intersections/Interchanges Within Project: 7.
AFCEC- Travis Air Force Base Repair Ramp 400 & Taxiway N, Fairfield California
Project Summary
Southwest Concrete Paving (SWCP) served as a key subcontractor for the Repair Ramp 400 Phases 2 and 3 and Taxiway November Project at Travis Air Force Base in California. The project consisted of the full removal and replacement of existing heavy-duty airfield concrete pavement. In addition to the primary airfield paving scopes, work included lime and cement modification to the existing subgrade, replacement of subbase layers with a cement stabilized drainage layer, hot mix asphalt shoulders, protection of existing fuel lines and hydrants, installation of new underdrain system with collection structures, new fiberglass monitoring well pits, grounding rods, and pavement markings. Initially, the project was designed to be completed in three separate phases of construction: Ramp 400 Phase 2, Phase 3, and Taxiway November. Since all three phases were adjacent, the Government amended sequencing to allow construction of the three phases to be completed concurrently. This change added benefits to the overall duration and constructability of the project; however, the original plans were designed by two separate entities, and no modifications were made to the plans reflecting these changes. Because of this, there were numerous challenges during the early stages of the project as discrepancies resulting from overlapping plan sets became more evident. These initial challenges were resolved through a combined partnering effort between the Government, base personnel, and the project team. The project was completed significantly ahead of schedule and under budget.
The new pavement section consisted of a new apron of 17.5-inch Portland cement concrete pavement (PCCP) on Ramp 400 and an adjacent 20.5-inch PCCP section on Taxiway November, each section separated by a thickened edge isolation joint. The pavement sections contained both new and existing utilities, which were to remain in place. Existing utilities that required protection during demolition and construction included: monitoring wells, storm drain cleanouts, fuel hydrants, high point pits, and utility markers. Slip form paving was constructed using a Gomaco GP4 Slipform Paver with Leica wireless controls for horizontal and vertical alignment. SWCP chose to pave the project at 37.5-foot paver width, which required a government-approved RFI to change the originally designed 18.75-foot-wide lanes to 37.5 feet in width. SWCP negotiated the change with the Government and simultaneously eliminated dowels in the longitudinal contraction joint created by the new configuration. In doing so, SWCP maintained consistent forward movement of the paver at 2.5 feet per minute with the 37.5-foot paving width in both the 17.5 feet and 20.5 feet in thickness paving sections while delivering concrete through belt placers positioned on both sides of the paver. The weather at Travis AFB did not provide much respite for the paving crew. Typical paving days saw an average of 20-30 mph high winds and hot weather during the summertime in Northern California. Paving shifts were shifted to 2 am start times to mitigate these conditions to maximize the least objectionable conditions typically present during a 24-hour cycle. Accomplishing this took significant communication with base security management (and a few lunches) for crews and delivery vehicles to gain site access during normal shut hours. This flexibility allowed for typical 2,000 CY production days to be done primarily under darkness and in lower daily temperature windows.
On-Site Batch Plant
An on-site batch plant was erected to facilitate the mixing and delivery of 1.25” to 1.5” slump (2.0” max) concrete for the project. The on-site plant utilized for the project was a central mix Rexcon Model SE Batch Plant equipped with four horizontal storage guppies for additional storage of cementitious materials. A 25,000-gallon water tank equipped with a 60-ton chilling unit was also mobilized to store and chill batch water. Concrete produced on-site was hauled to grade in open-bed, ten-wheel dump trucks and deposited in front of the paver using two belt placers. Project specification requirements did not allow the concrete to be dumped on grade directly in front of the paver, so Gomaco RTP placers were used simultaneously from each side of the paver to support the primary 37.5-foot paving width. With the plant site inside Travis Air Force Base, material delivery was strictly managed to maintain supply with project demand. In addition, airfield and site optimization were critical to minimizing base impact and keeping the throughway safe.
Project Information
Timeline: 7/20-10/21
Total Square Yards of Paving: 51,000 SY
Total Lane Miles: 2.5 Miles
P-596 North Ramp Apron and Hangar 95 MCAS Yuma, AZ
Project Summary
Southwest Concrete Paving (SWCP) served as a key subcontractor for the P-596 North Apron and Hangar 95 Reconstruction MCAS Yuma. The project involved two worksites within active areas of the airfield. The Hangar 95 worksite included a complete renovation of the hangar with the associated removal and full-depth repair of the adjacent F35C parking apron. The north apron worksite, which houses rotary-wing aircraft, expanded the apron and included a full-depth removal and replacement of adjacent Taxiway Bravo (B) across its entire width, directly abutting the north apron. A smaller area of adjacent Taxiway Charlie (C) that exhibited significant cracking and poor serviceability was also removed and replaced full-depth as part of the north apron project.
Both worksites required a cement-treated base (CTB) course and Portland cement concrete pavement (PCCP). SWCP batched and placed two 6-inch lifts of CTB at the Hangar 95 apron before mobilizing to the north apron, where a single lift of 8-inch CTB was batched and placed.
After CTB installation at both sites, SWCP began batching and placement of PCCP on the north apron site, which required an accelerated schedule to accommodate the annual base training and airshow scheduled for late August through October. All work was required to be completed and turned over before the show, with the exception of striping, which was allowed to be temporary. Upon completing the north apron worksite, SWCP completed PCCP at the Hangar 95 site.
North apron activities were conducted at night, creating challenges for truck access to the base as contractor gates were not open. SWCP negotiated a two-load allotment of cement deliveries each night to sustain operations until the remaining loads could be delivered at 6 am. During construction, airfield operations were technically shut down between 12 pm and 8 am; however, unannounced aircraft would arrive periodically and temporarily block access through the live taxiway.
Unique Features
The north apron site included significant portions of Taxiway B that required closing during construction. These closures meant all traffic had to be routed through Taxiway C, creating a potential bottleneck for airfield operations and trucking crossing the same area continuously throughout the day. Foreign Object Debris (FOD) management was a significant part of the project, especially during CTB placement during daytime hours. Concrete paving night operations helped minimize impact during that phase of work. In addition to these logistical issues, the north apron had an extensive volume fuel line that ran the length of the apron. This fuel line was active and critical to activities, requiring protection during construction. Contract requirements limited vehicles to50 psi when crossing the fuel line during construction.
On-Site Batch Plant
SWCP was able to set up an on-site batch plant to deliver concrete to both worksites. Because the batch plant was located in a known contaminated area, SWCP was restricted from digging at the site without prior soil testing on the spoils. Five electrical poles ran overhead power to the plant for operation, and an existing asphalt parking lot was utilized for stockpiling aggregates.
The batch plant was a Rexcon Model S Central Mix Plant with three horizontal storage guppies for additional storage of cementitious materials. Concrete was hauled to grade in open-bed ten-wheel dump trucks and deposited in front of the paver using a belt placer. The north apron site was approximately 12 minutes from the plant, requiring haul trucks to cross an active taxiway and stop for FOD checks. The Hangar 95 site was roughly half the distance from the plant, but trucks still had to ingress and egress through an operated security gate and cross an active fire lane with continual FOD checks.
Project Information
Project Timeline: 6/21-9/21
Total Square Yards of Paving: 61,000 SY
Total Lane Miles: 3.10 Miles.
USAF- Repair Taxiway To Pad 5 - Kirtland AFB, New Mexico
Project Summary
Southwest Concrete Paving (SWCP) served as a key subcontractor for the Repair Taxiway to Pad 5 Facility project at Kirtland Air Force Base in Albuquerque, New Mexico. The project consisted of removing and replacing an existing heavy-duty airfield concrete pavement taxiway and associated hot mix asphalt shoulders containing both flush-mounted and above-ground airfield lighting. This taxiway served as the sole feeder route to Hot Cargo Pad #5 utilized for loading and unloading live munitions onto aircraft. The Hot Cargo Pad itself was completed in a later supplementary project.
Paving
Concrete paving for the project consisted of placing 16-inch-thick airfield concrete utilizing UFGS criteria in section 32 13 11. The paving section was approximately 2,100 LF with a crowned centerline having a constant 1% fall to each side of the center. The taxiway section was arc-shaped, making a 90-degree turn over approximately 1,600 feet of its length. The taxiway terminated with a temporary loading pad intended for mission deployment while the adjacent Pad 5 was constructed. The alignment of the main taxiway also spanned Randolph Avenue, which is used as a primary thoroughfare for local vehicular traffic. Transverse contraction joints were dowelled, with baskets being utilized and placed pre-shift, as concrete was delivered in front of the paver utilizing a belt placer situated outside the paving lane. Construction joints were dowelled using the drill and epoxy method. Paving for the project was done using a four-track Wirtgen SPi-94 paver. Four primary paving lanes were 18.75 feet in width for a total taxiway width of 75 feet. Paver alignment for both horizontal and veritcal control were established and maintained using a Leica wireless system. A Minnich auto vibe system was utilized to monitor and control vibration.
Unique and Innovative Measures Employed by SWCP include:
• Stringless slip-form paving technology with the Gomaco Wirtgen SPi 94 through curved horizontal alignment.
• A 12-CY Rexcon Model S Central Mix Plant was nestled into a tiny plant footprint, allowing for on-site batching of materials and shortening delivery times.
• Sourcing aggregate from a significant distance outside the local area to guarantee the use of high-performing material.
• Mobilization of a pugmill to batch aggregate base course from constituent materials, overcoming the challenge presented by local suppliers unwilling to custom crush.
• Utilization of an asphalt paver to place aggregate base course to meet tight tolerance for line and grade of base course for the project.
• Overcoming a challenge early in the project, brought on by locally supplied materials which made entrained air generation in mixture extremely difficult.
• Utilization of existing mix design with modifications to optimized blended aggregate matrix
Unique Challenges / Solutions
• Overcame a local materials issue and worked with admix supplier to modify admix delivery system to help generate entrained air in the concrete.
• Worked with fly ash suppliers to overcome unplanned outages at the generating station supplying fly ash for the project. SWCP performed ASR testing with a secondary source and received approval for source change with submitted results.
• Overcame scheduling challenges presented by picking up a job contract nearing liquidated damages. SWCP finished the project on time with superior quality.
• SWCP and its prime contractor discovered a bust in the plan grades during the construction of the job and worked with the design team to field fit a solution that worked for both drainage and constructability.
Project Information
Project timeline: 1/2018-6/2018
Project Length: 0.41 Miles
Total Square Yards of Paving: 23,080 SY