Repair Taxiway Bravo Ramp (WAK008) and Repair Hot Cargo Pad (WAK006)
Project Summary
Southwest Concrete Paving (SWCP) served as key subcontractor for the Repair Hot Cargo Pad and Repair Bravo Taxiway (WAK006 & WAK008). The project was awarded as a design-build project to AECOM and included two different sites on a military base at Wake Island. The USAF maintains an active base on Wake Island, a tiny atoll island located approximately 2,500 miles west of Hawaii. The base encompasses the entire island, with access to the island restricted to those actively stationed on base or federal contractors working on active projects. Travel to the project location itself was a long and cumbersome journey that required a chartered flight from Honolulu to the island, typically a 4-5 hour flight. These flights, scheduled only every two weeks, brought in a limited number of supplies along with a fresh crew while another crew departed off the island to return home for a short break. The airfield consists of a 10,000-foot-long runway and an adjacent taxiway, Taxiway Echo (E). Taxiway Bravo (B) is adjacent to the main Taxiway E and connects at the other end of Taxiway B to Taxiway Alpha (A). Just off Taxiway E, on the other end of the runway, is the Hot Cargo Pad, which is used as a parking/staging area for aircraft carrying hazardous cargo. The project involved replacing the existing asphalt on both Taxiway B and the Hot Cargo Pad with heavy-duty airfield Portland concrete cement pavement (PCCP). Due to the extreme remoteness of the project, SWCP carefully planned every aspect of the project to ensure that the project was a success. Most of the project materials needed to be barged in from the mainland U.S., including all aggregates and required material for construction and temporary housing, construction and batching equipment, and a water filtration system for construction water and the batch plant. SWCP was highly cautious with the quantities, not exceeding the allocated materials and not bringing excess material due to the remote location and subsequent costs.
SWCP utilized a GOMACO 9500 equipped with a trimmer head and a Leica Stringless 3D system to maintain quantities and make a final cut on our subgrade before laying PCCP. However, as paving operations began and the GOMACO 9500 was needed as a placer, SWCP could better utilize the motor grader to finely grade the subgrade before paving.
Along with demolishing the existing asphalt taxiway and Hot Cargo Pad, the subgrade, mainly of native soil and crushed seashells, had to be mechanically stabilized. The batch plant location was on the base, just off the airfield, which already had limited access. Having the batch plant so close to the Taxiway B project location meant a quick turnaround at the plant. The hauling time significantly increased once PCCP on Taxiway B was completed and paving operations moved towards the Hot Cargo Pad. Fortunately, SWCP was able to coordinate with personnel and other construction operations on base to maintain a reasonable traffic plan.
Most paving activities took place at night to reduce interference with airfield operations. However, to counteract the effects of the constant rain and weather delays, construction crews ran continuously for 24 hours, rotating between a day crew for grade preparation and clean up and a night crew for concrete paving operations. SWCP superintendents often worked longshifts to ensure a proper hand-off from the day crew to the night crew and vice versa. This seamless transition relied on precise scheduling, constant contact with airfield operations, and diesel-powered light plants at night. In addition to the new PCCP for the taxiway and Hot Cargo Pad, a PCCP shoulder was also placed. Upon completion, grounding rods and tie-downs were installed along both project areas for various aircraft. The work scope also included the removal and reconstruction of a dual 24-inch RCP storm drain line which connected the main drainage basin from the airfield to the bayside of the ocean, an electrical lighting system, and the final step striping the new PCCP
On-Site Batch Plant
SWCP mobilized a low-profile batch plant to set up on the island. The low pro-plant was selected because of its self-erect capability, which did not require a crane for erection. Despite this option, SWCP chose to fabricate and install a 4-foot riser on the plant requiring a small on-island crane to set the drum. All cementitious materials were mobilized to the site in one phase. These products were transported in super sacks, and the entire project was paved using sack unloaders to transfer cementitious material from the super sacks to on-site storage guppies.
Sustainability Measures, Including Economic and Environmental Factors:
Because of the project's remote island location, waste had to be carefully captured and boxed for return and disposal on the mainland. The ternary cement used on the project was significantly more environmentally friendly than typical cement. The combination of 15% limestone and 50% slag into the blend significantly minimized the amount of type II cement and significantly reduced the carbon footprint required in the manufacturing process. The utilization of on-site coral as the bedding and base material was an effective means of constructing the project.
Unique and Innovative Measures Employed by SWCP include:
•Stringless slip-form paving technology with the Wirtgen SP 94i with 20’ wide paving lanes reduced job site congestion and improved both horizontal and vertical concrete placement control.
• A 12-CY Rexcon Model S Central Mix Plant, which provided the highest quality concrete for this project.
• Coordination of activities with base personnel to maintain active airfield operations.
• Paving for the project was done primarily in the spring and summer season, although temperature fluxuation remained relatively low between seasons and did not play a role in concreting operations. The most significant impact to the schedule was rain. As this project is located in a tropical location which can provide more than 30 inches of rainfall in the rainy season, from April to November. It was typical to receive some rain almost every day.
• Using bag unloaders for cement dispersion was a challenge throughout the job. A separate shift had to be utilized each day to prepare for the paving shift in order to unload sufficient material to maintain schedule.
Unique Challenges / Solutions:
During our pavement operations planning process, SWCP worked closely with the on-site AECOM management as well as the Iowa-based design team to overcome challenges on the project. Working with and having a great relationship with the designer, SWCP provided a more suitable design and a better finish product for the customer. This better-quality product required substantial quality control in both the planning and execution of the paving plans and accurate survey measurements of the existing conditions. Weather played a significant factor in the schedule of this project. Although not necessarily delaying the paving schedule, there were months of weather-related delays in other areas. Higher than average winds, which prevented the barge from unloading materials and aggregates, plagued the first few months of the project. By executing an aggressive yet workable schedule, SWCP finished pouring concrete earlier than anticipated. This early completion was made possible by the quality control team and field superintendents' commitment to quality, ensuring only the highest quality PCCP was placed. The project was completed with 2-panel replacements out of over 100,000 square feet of PCCP. The Covid-19 pandemic began just before production was to start. The USAF personnel and leadership on the island worked with us to continue the project. SWCP was able to adjust the crew schedule and team rotations to provide such safe guards to prevent any out breaks of Covid on the island, keeping all personnel safe and maintaining the project schedule during a difficult and uncertain time.
Project Information:
Total Square Yards of Paving: 104,000 SY
Project Timeline: Novemeber 2019- December 2020
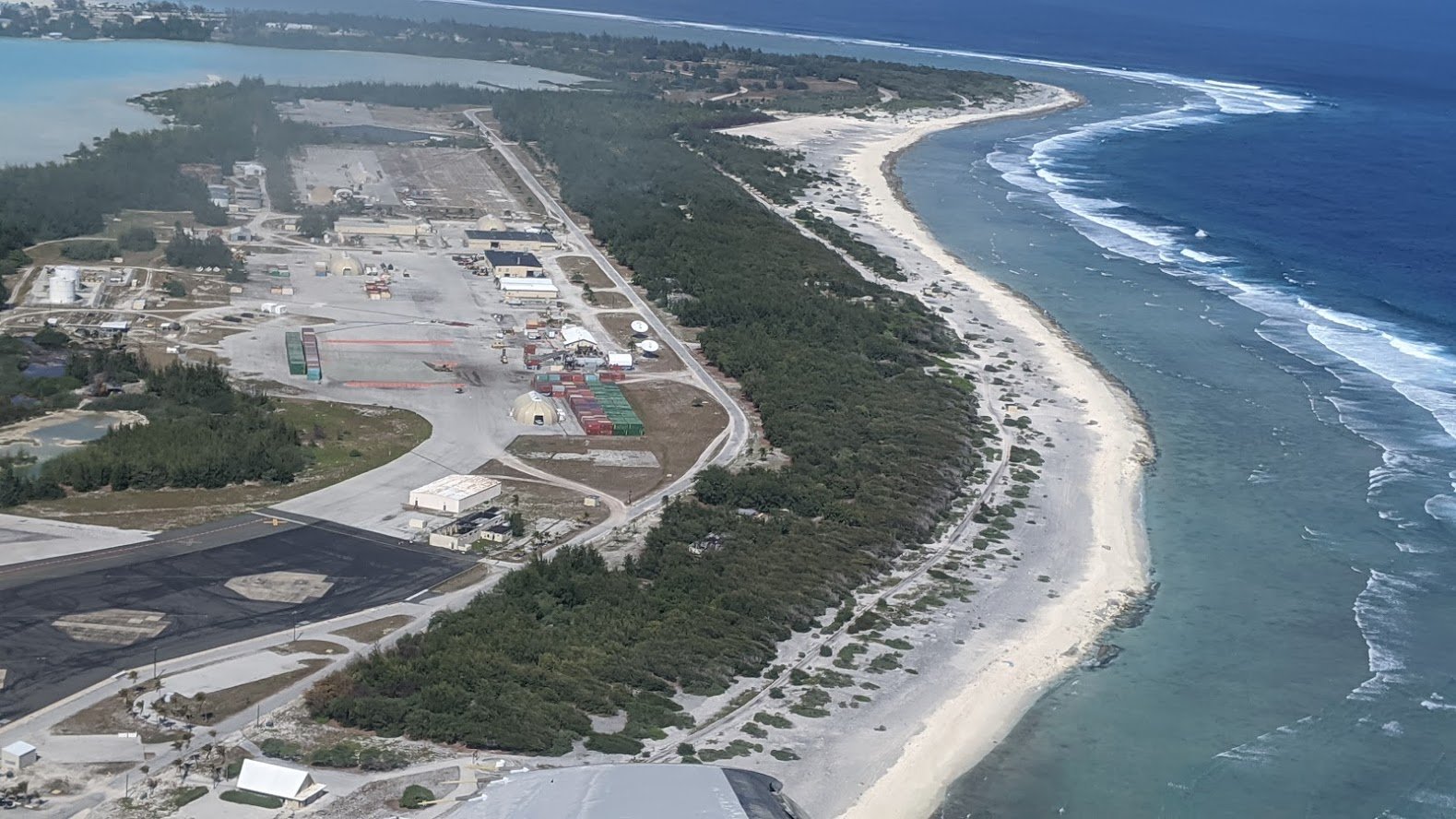

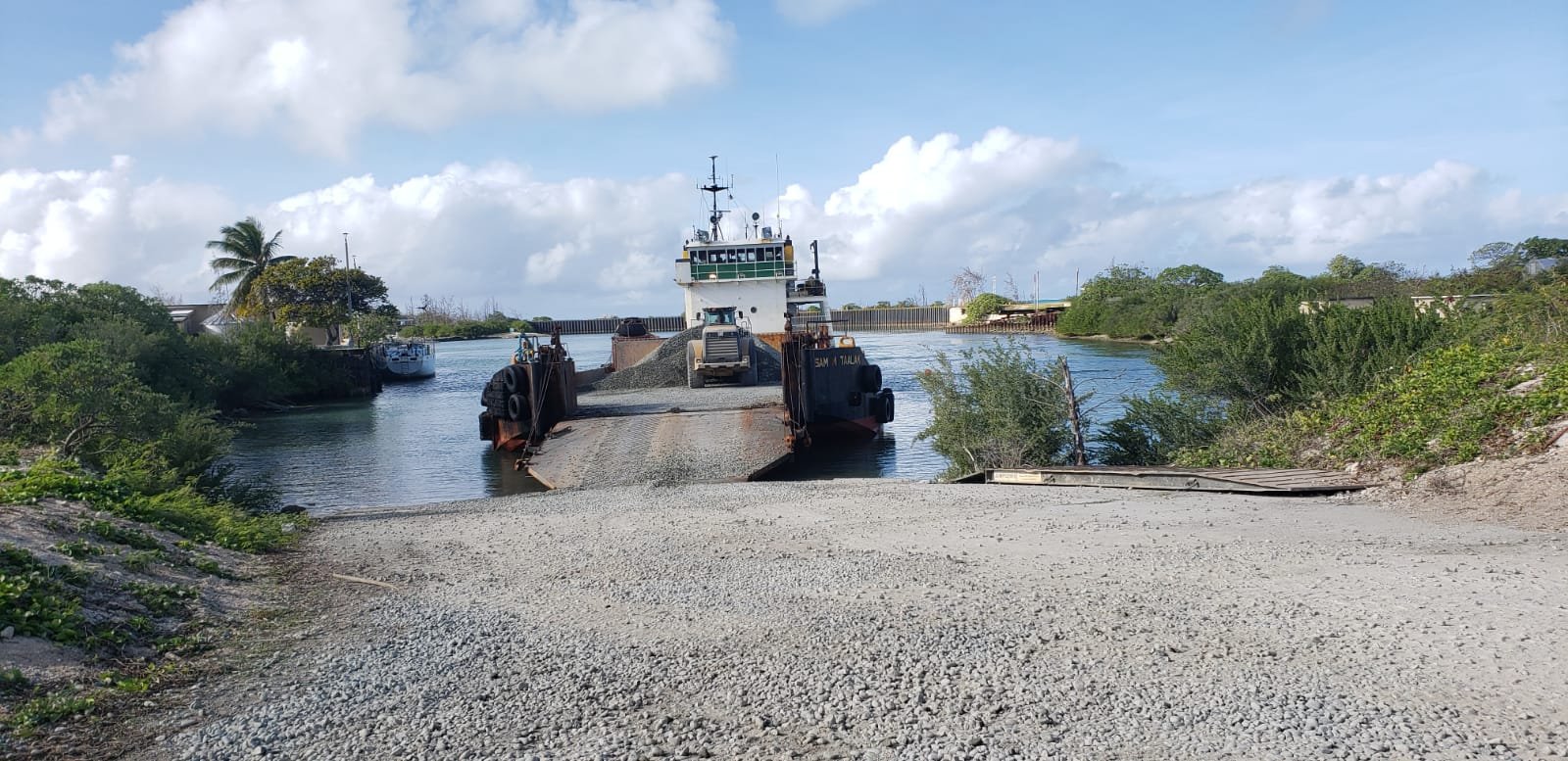
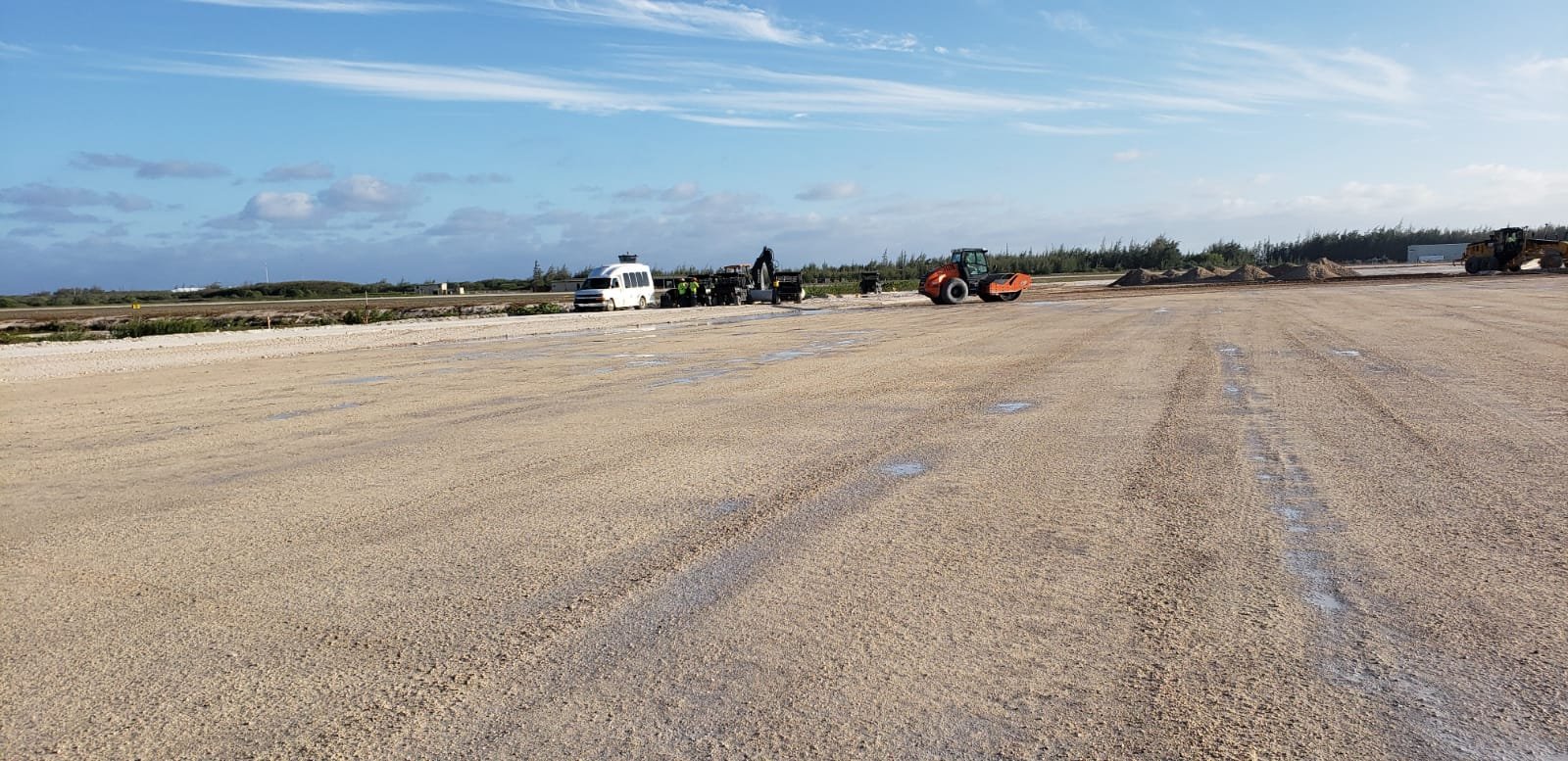
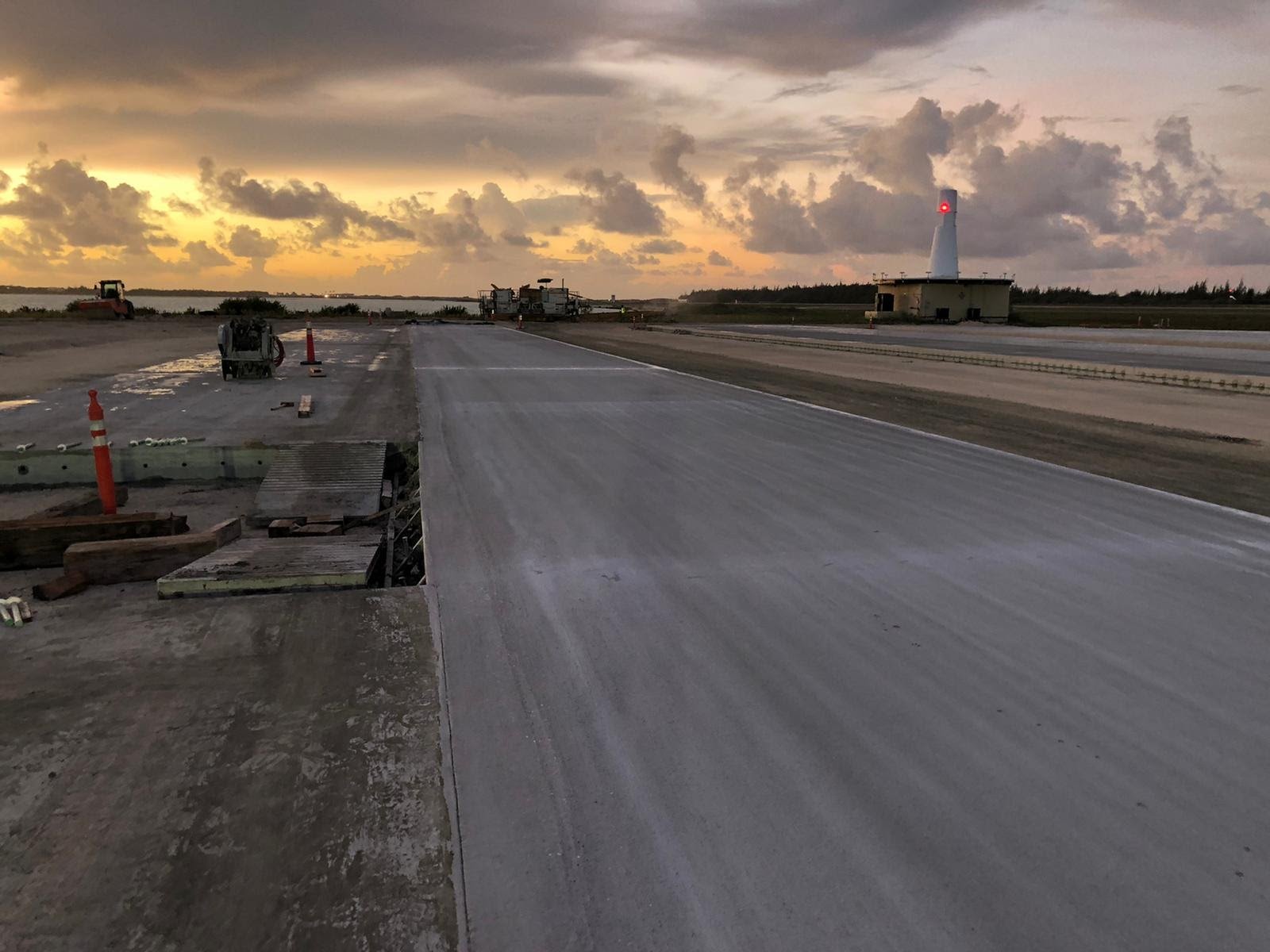
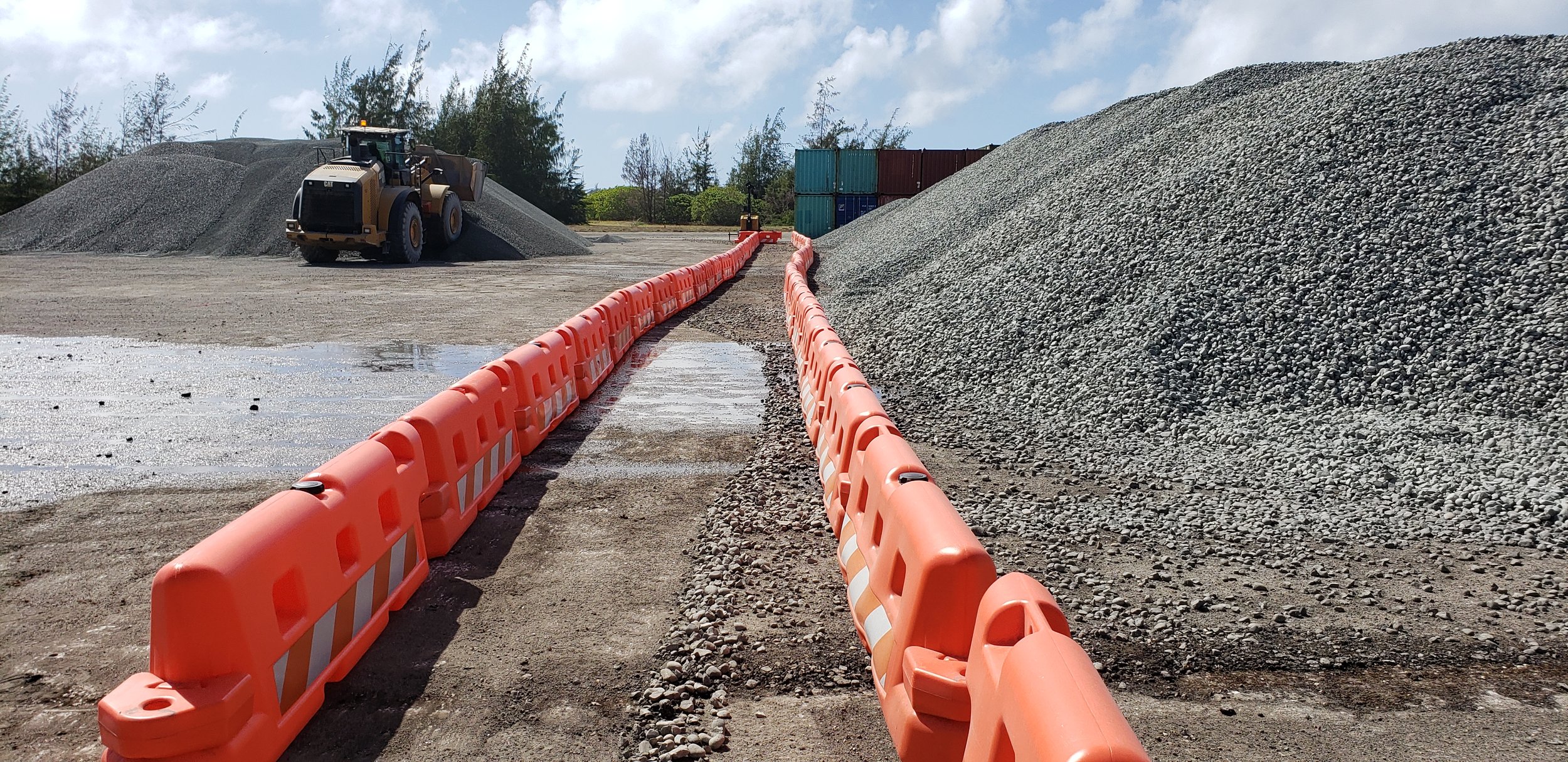
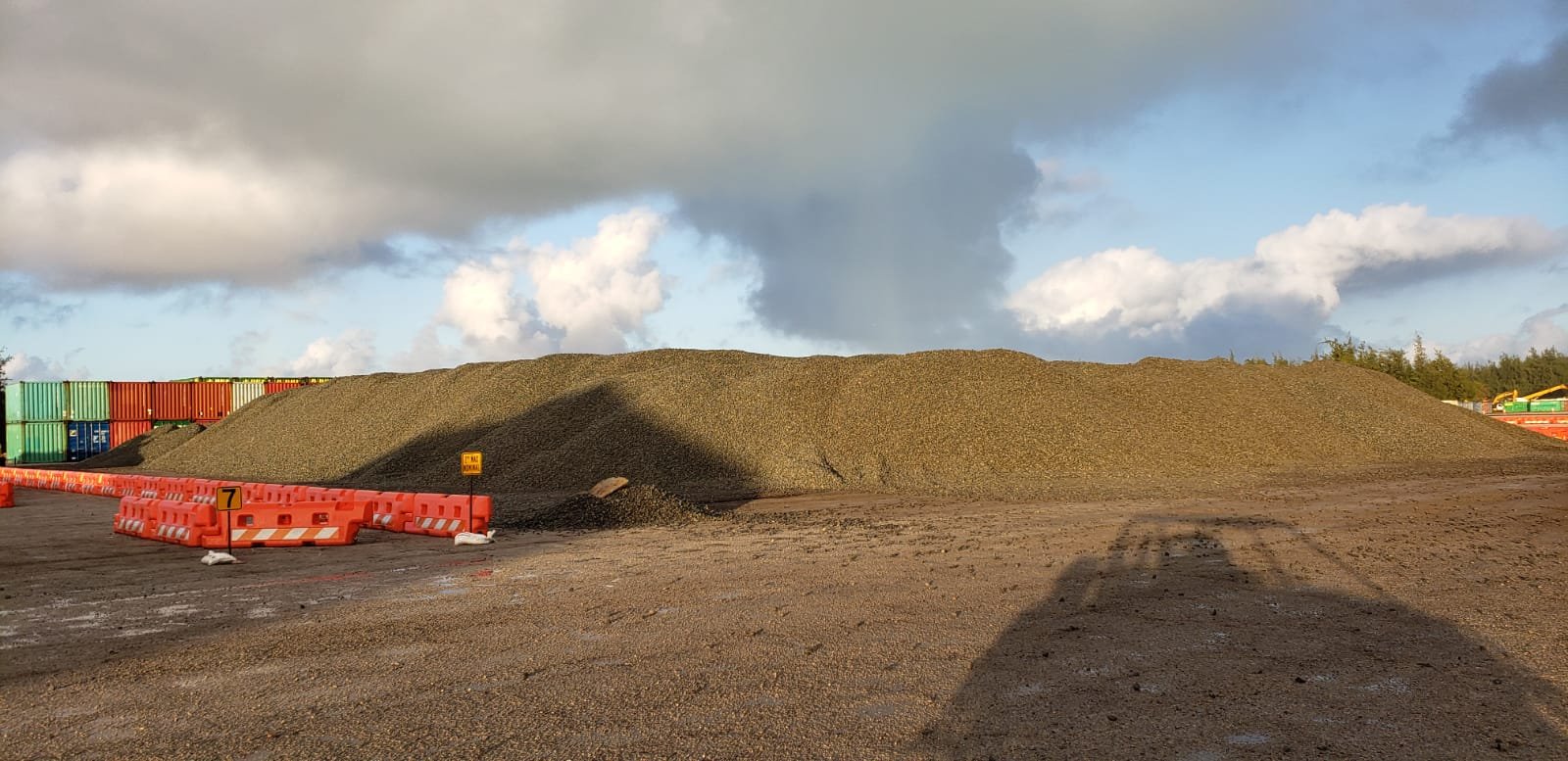
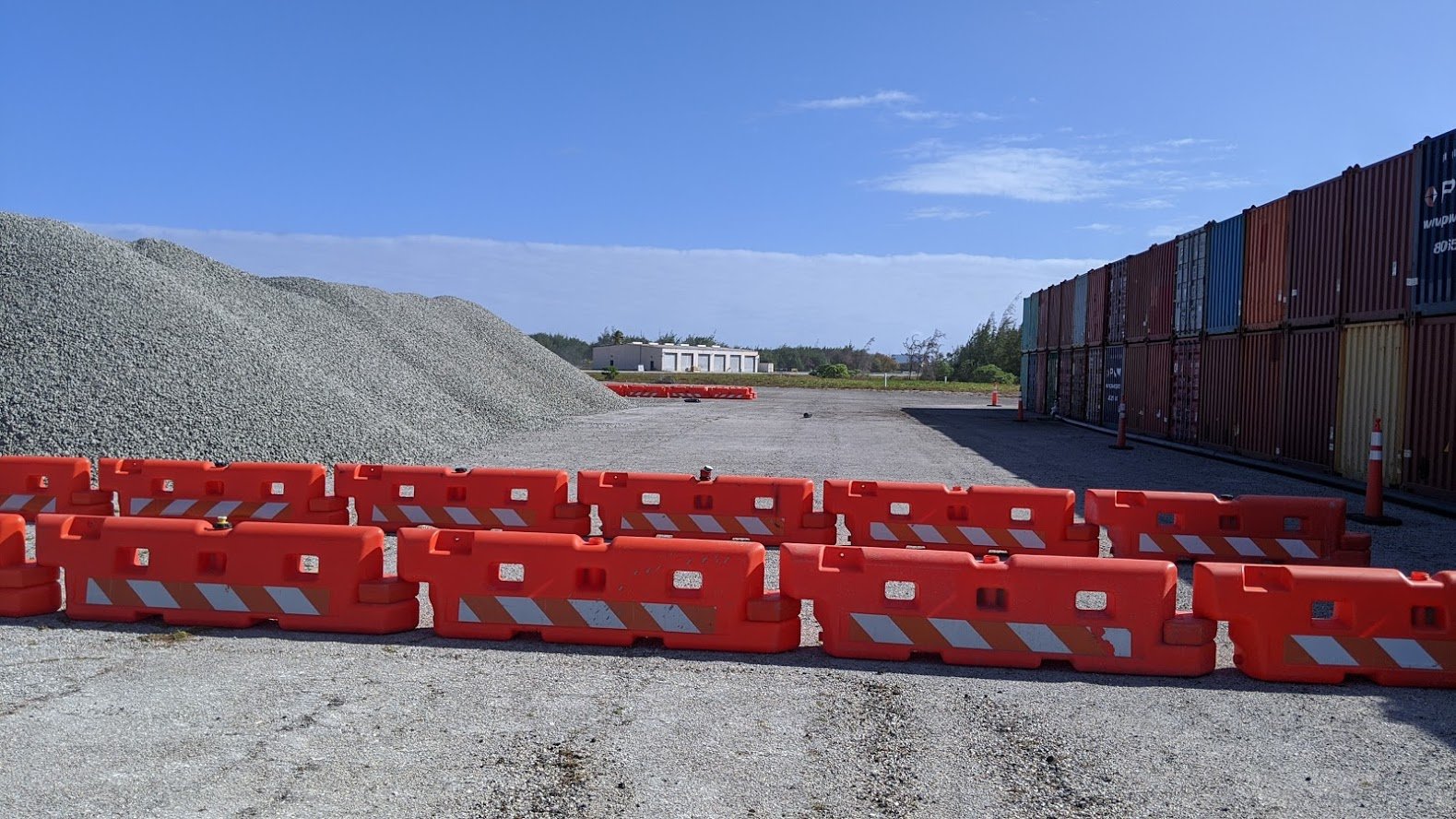
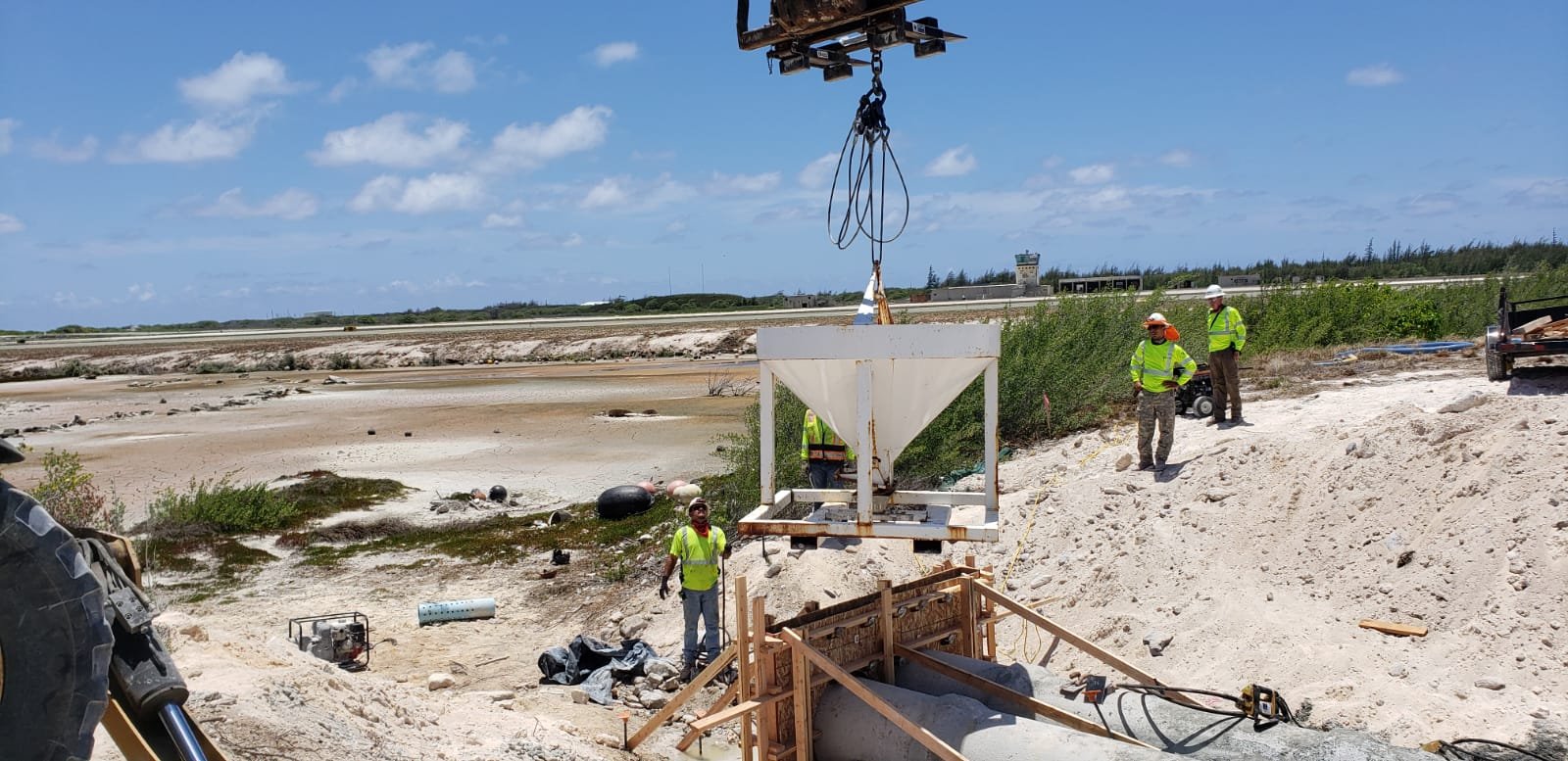
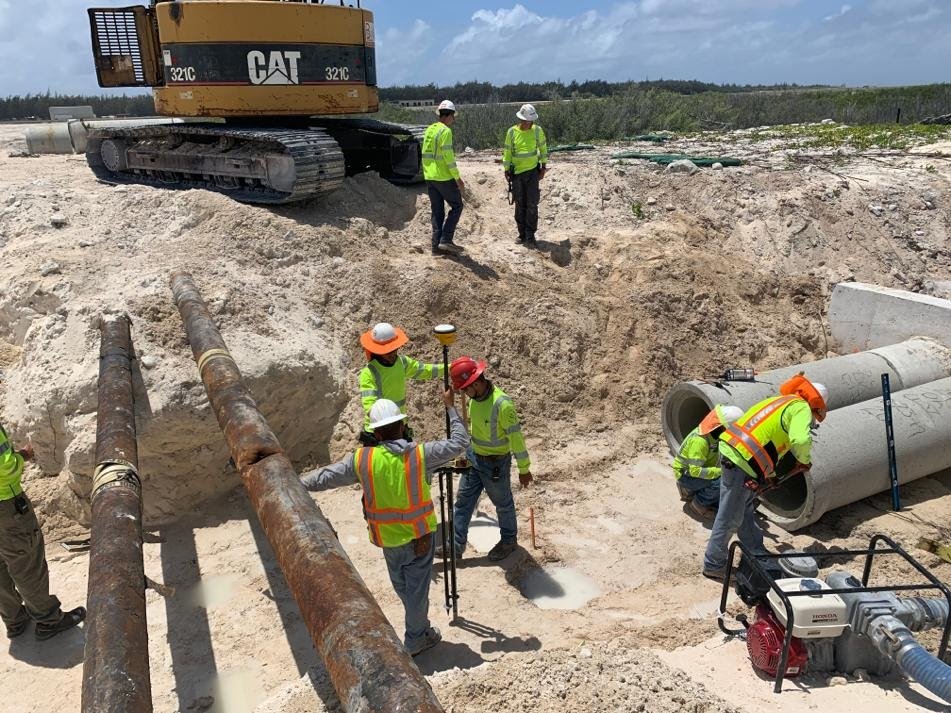
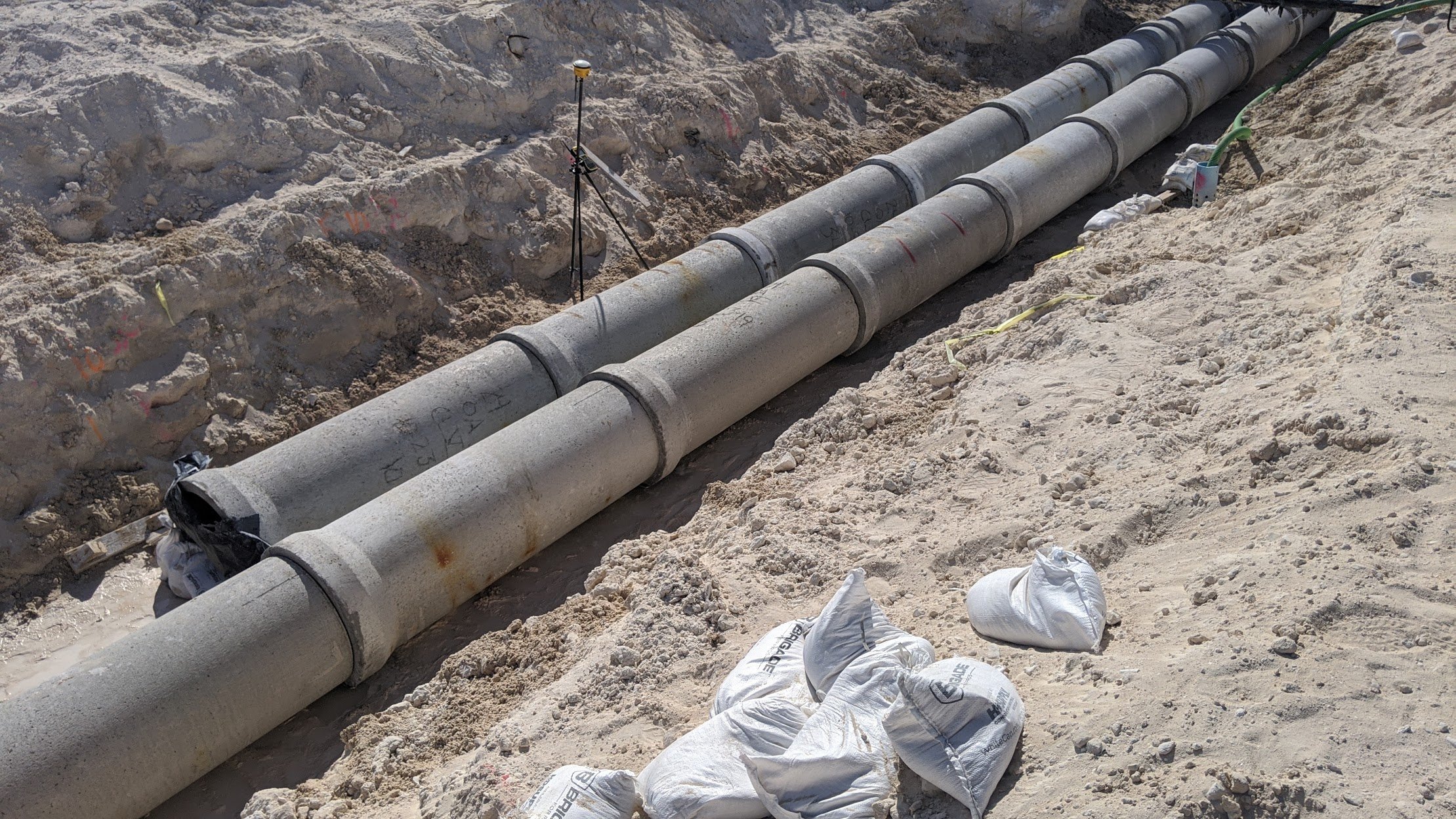
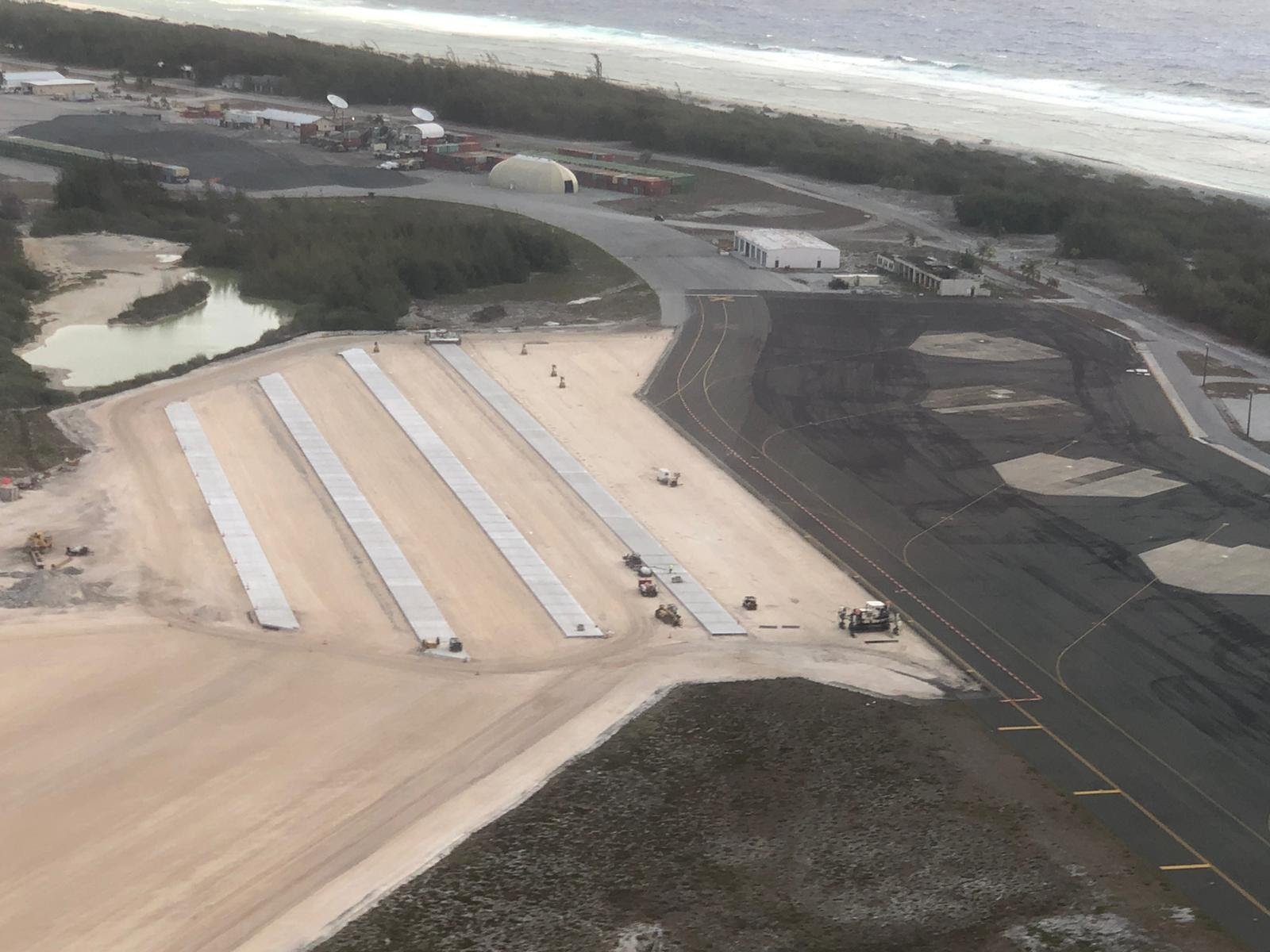
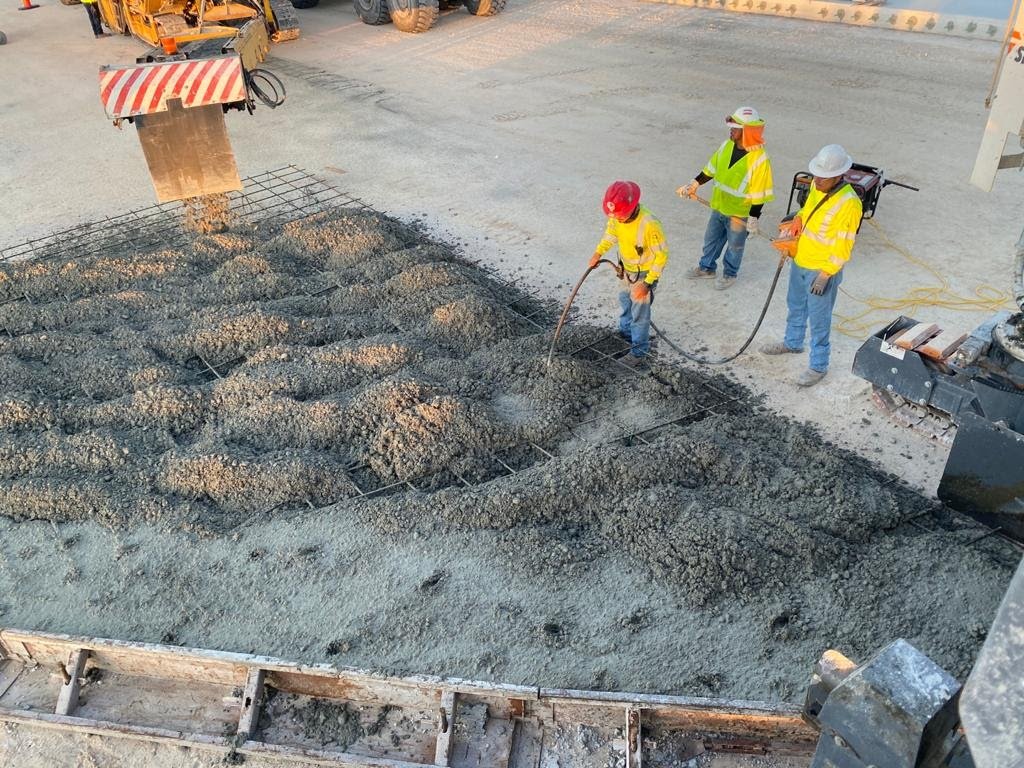
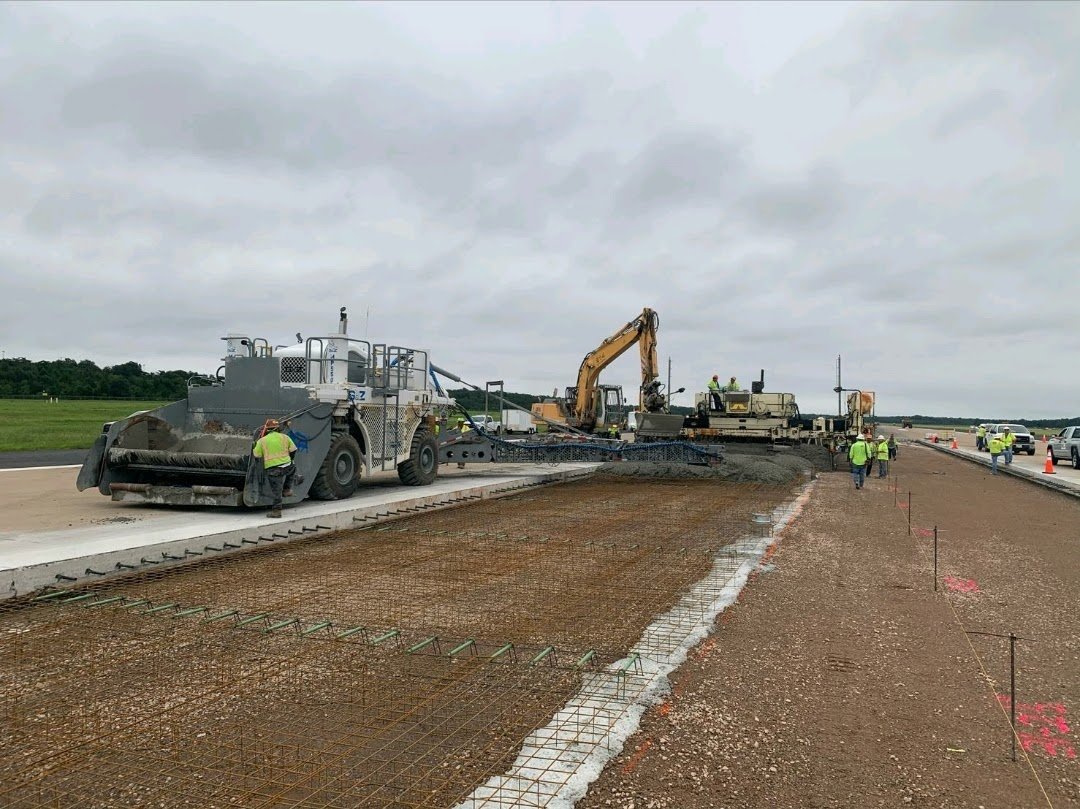
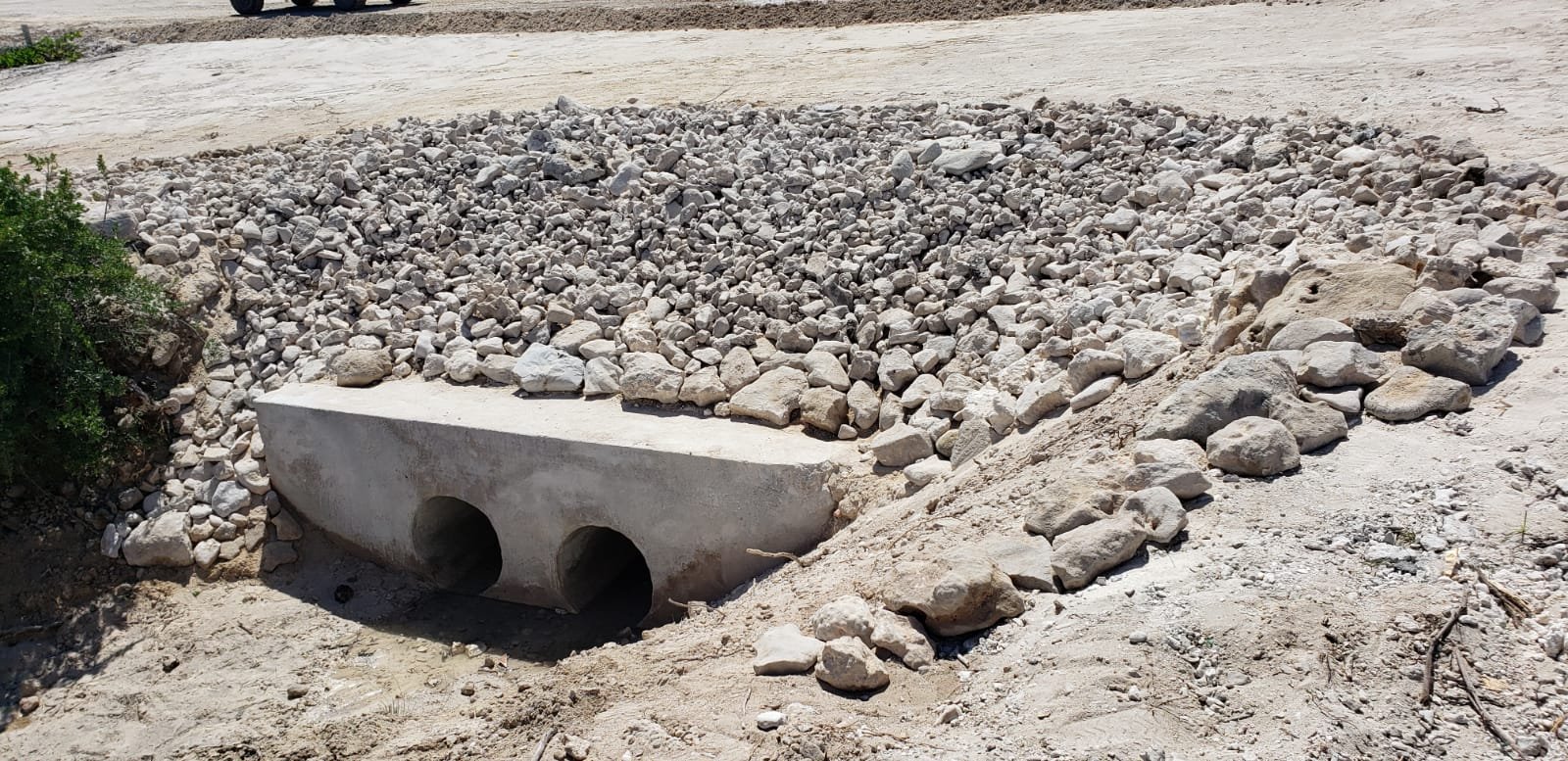
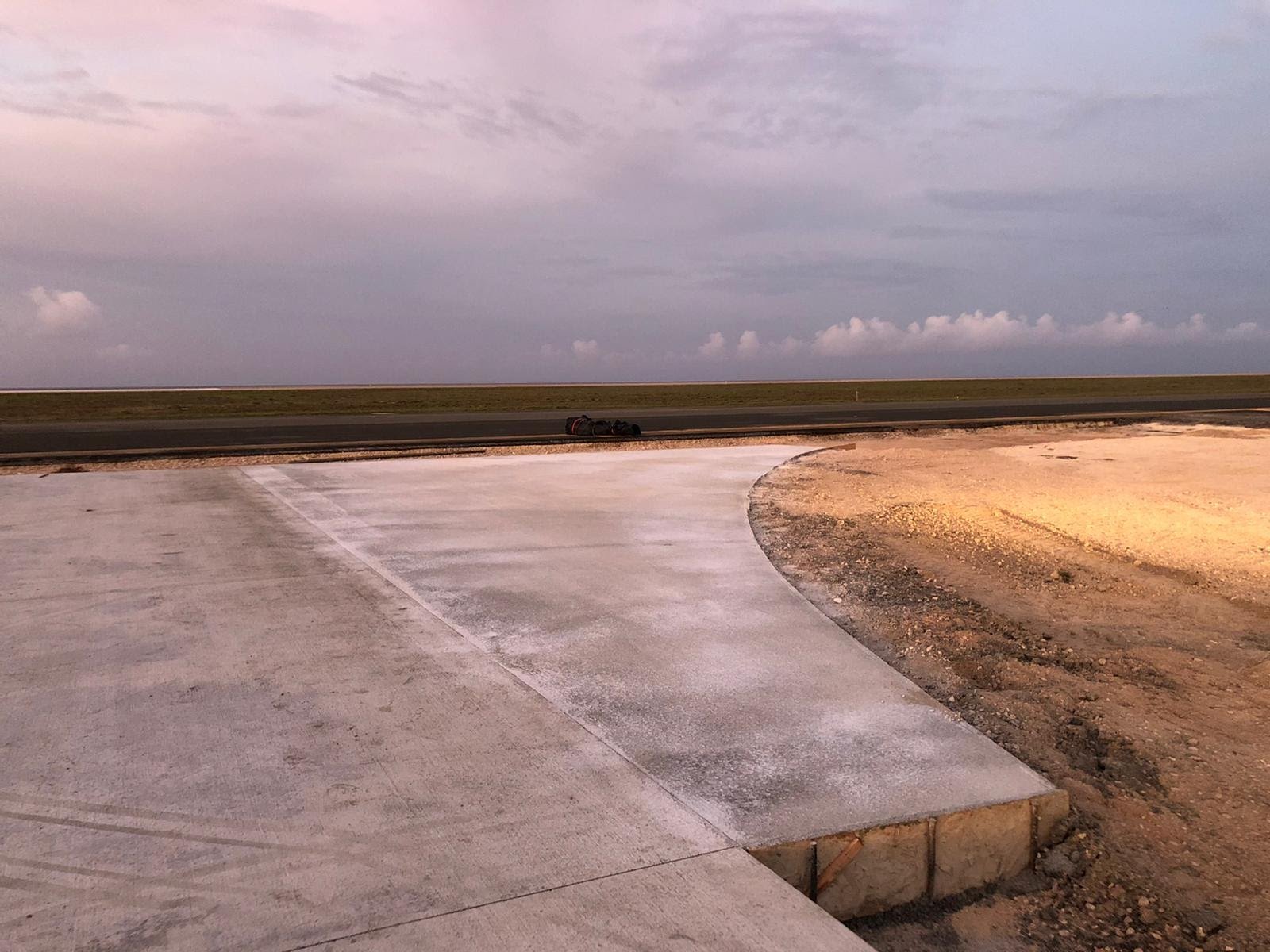
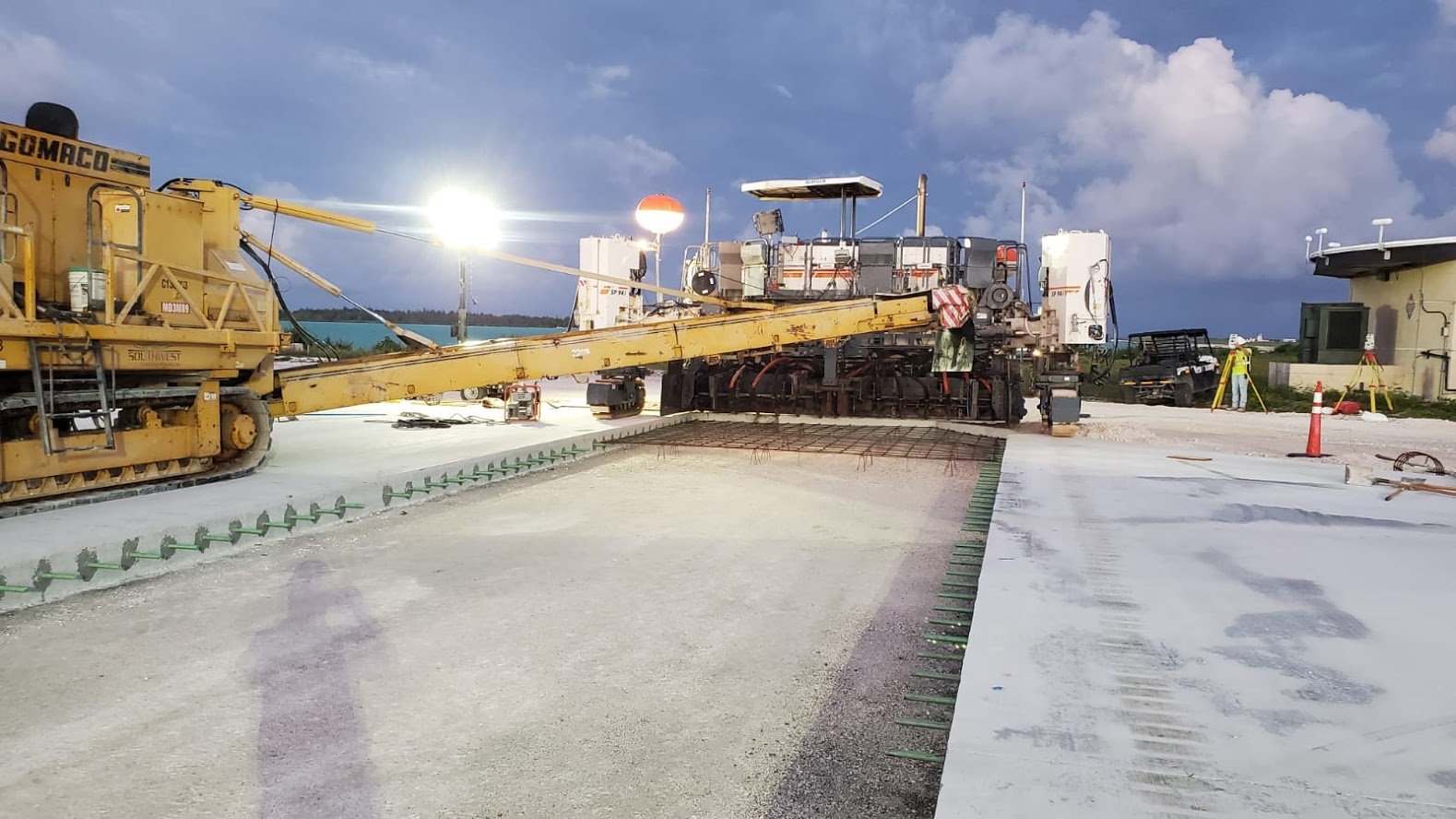
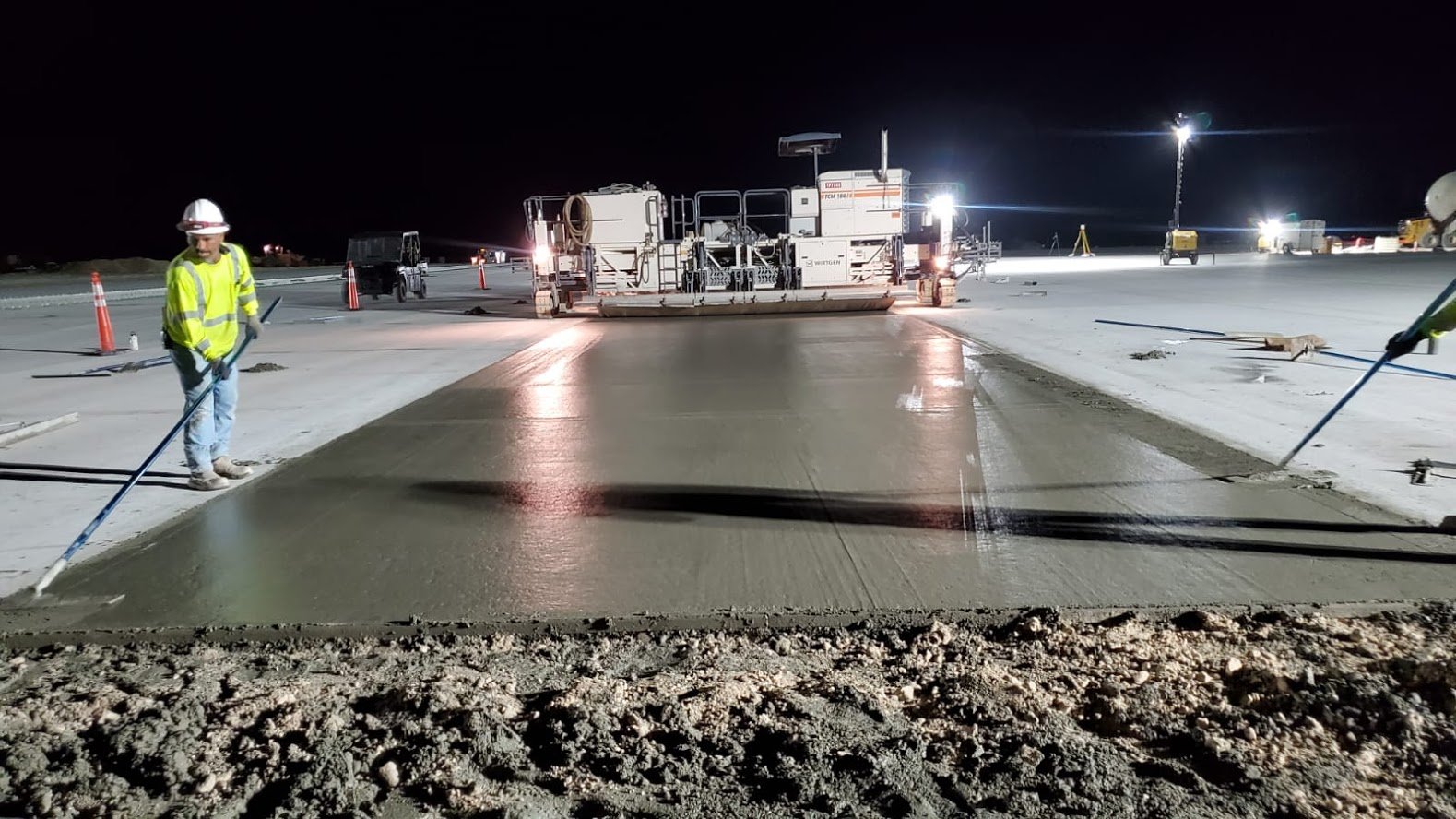
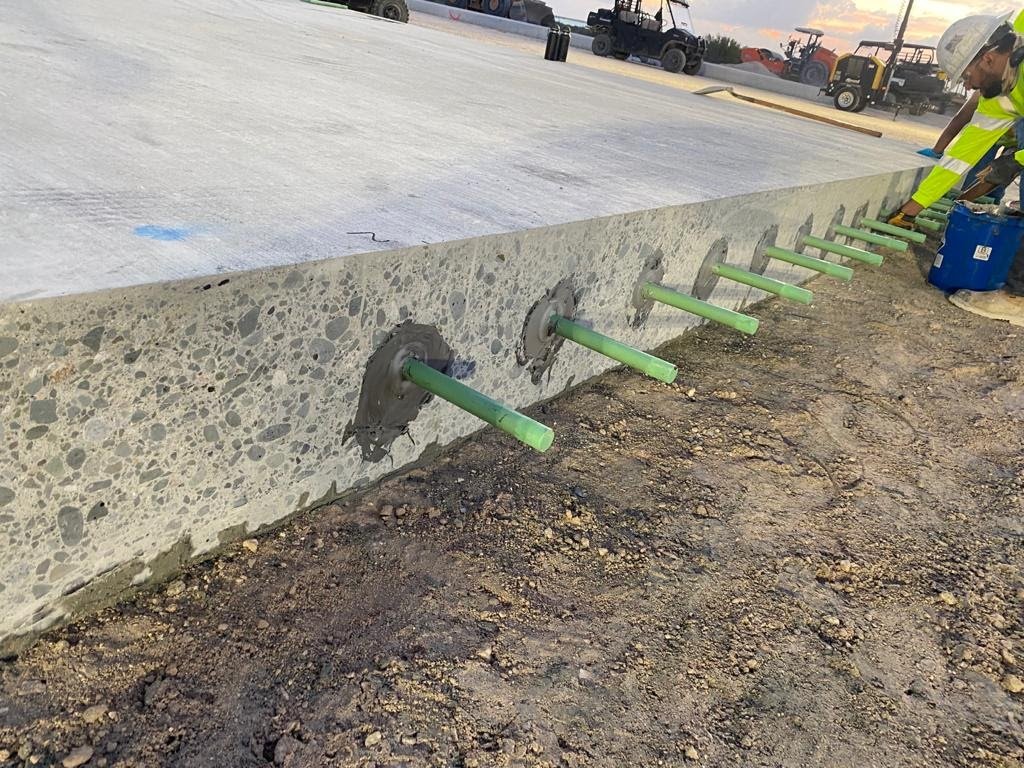
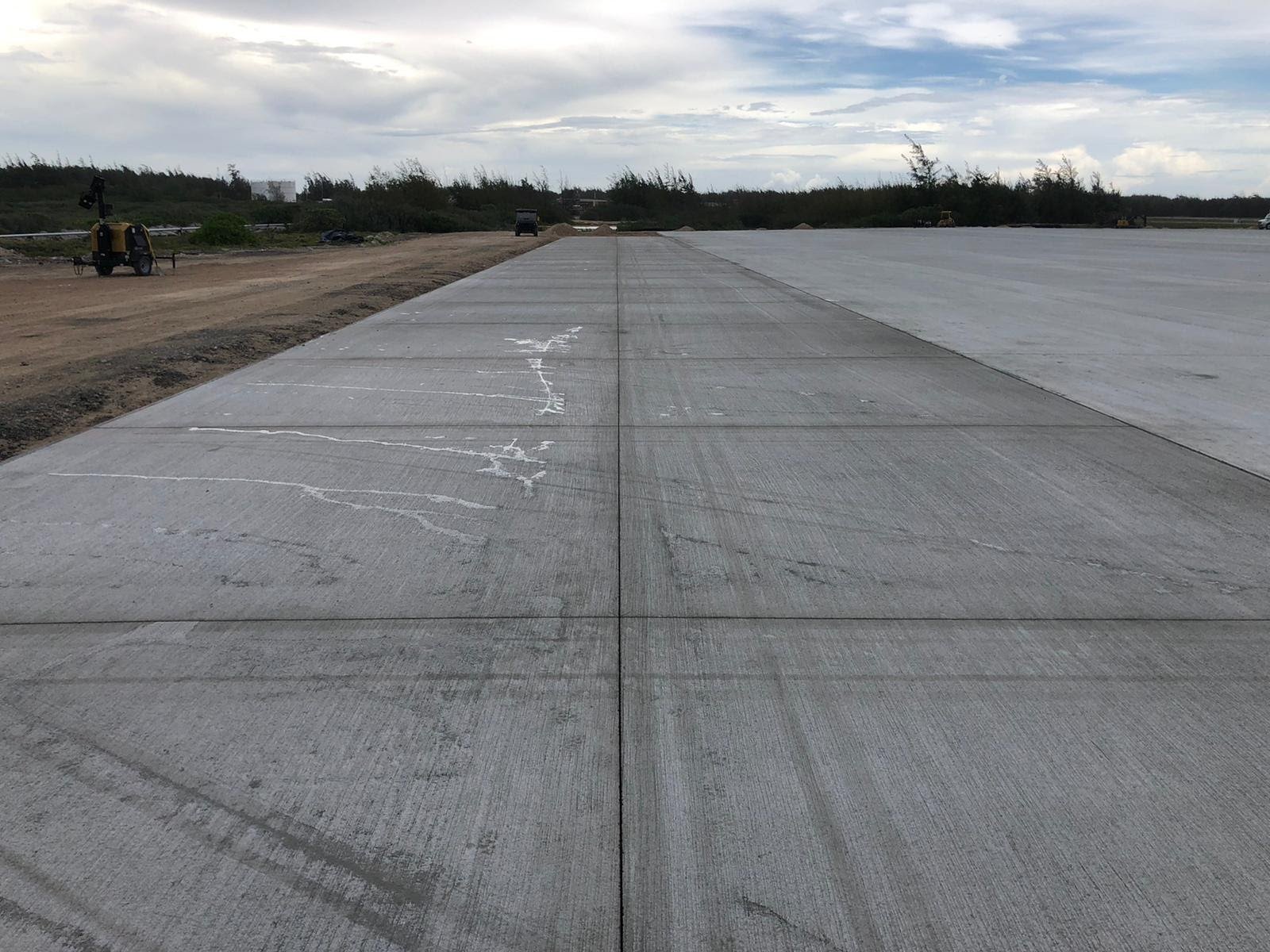
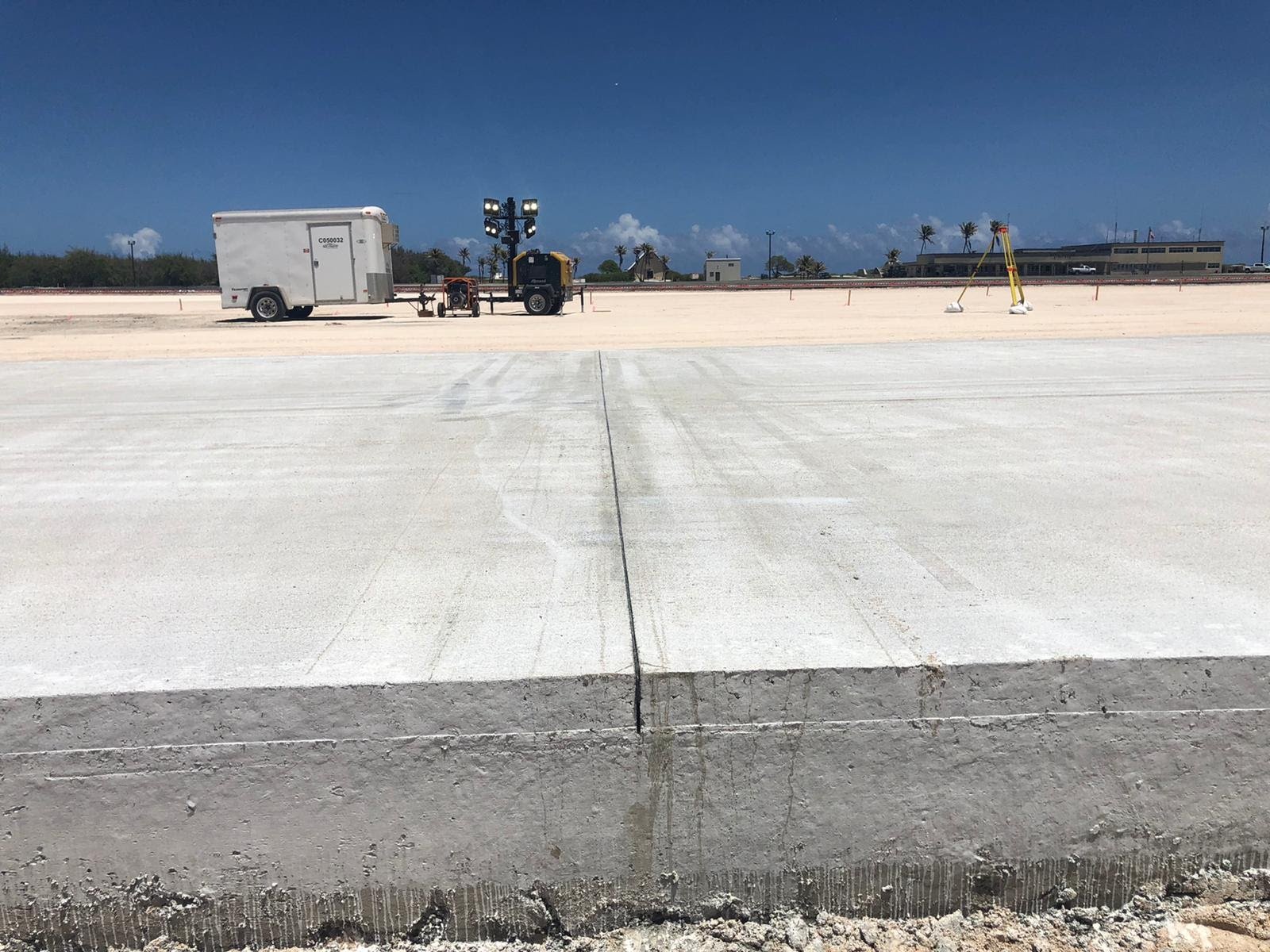
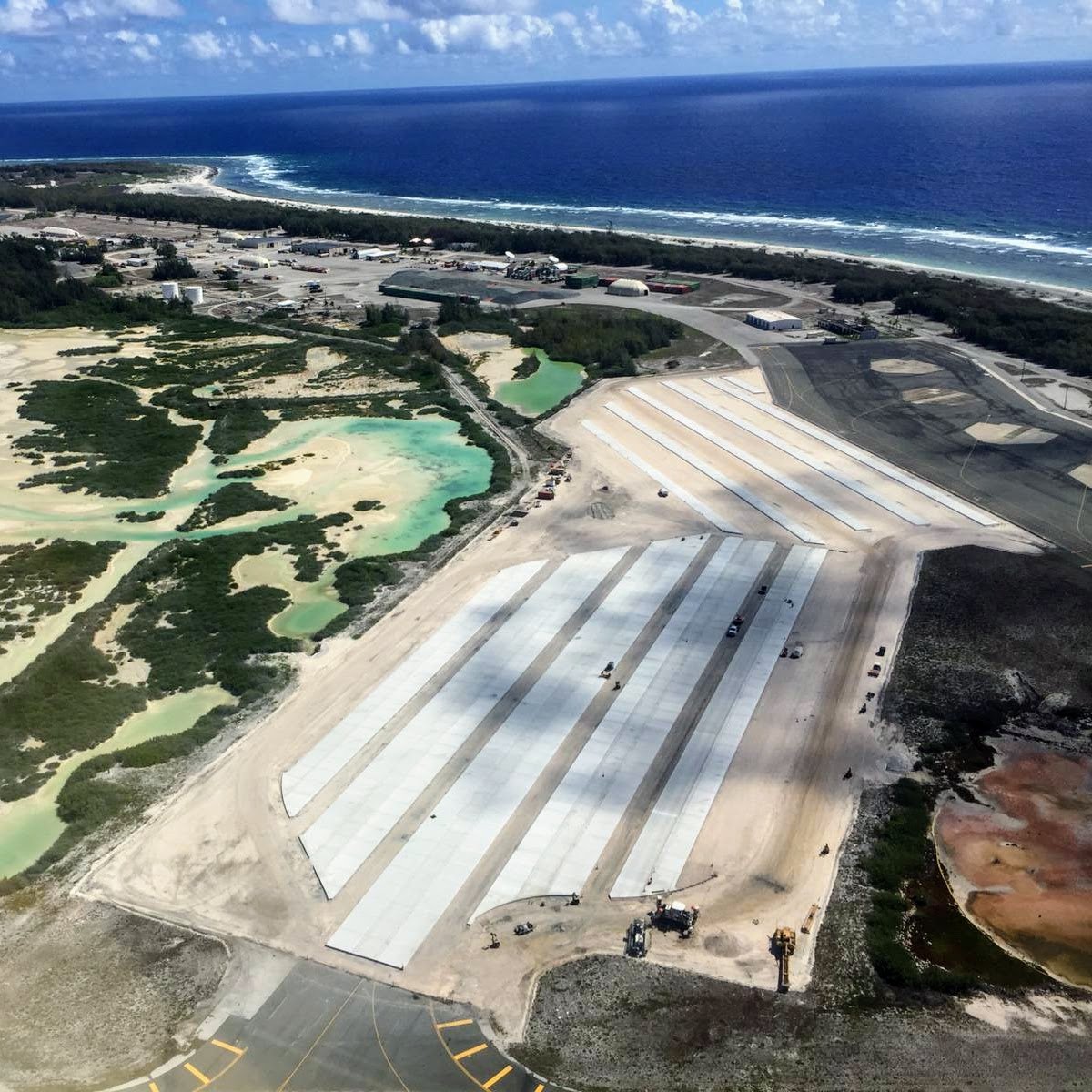
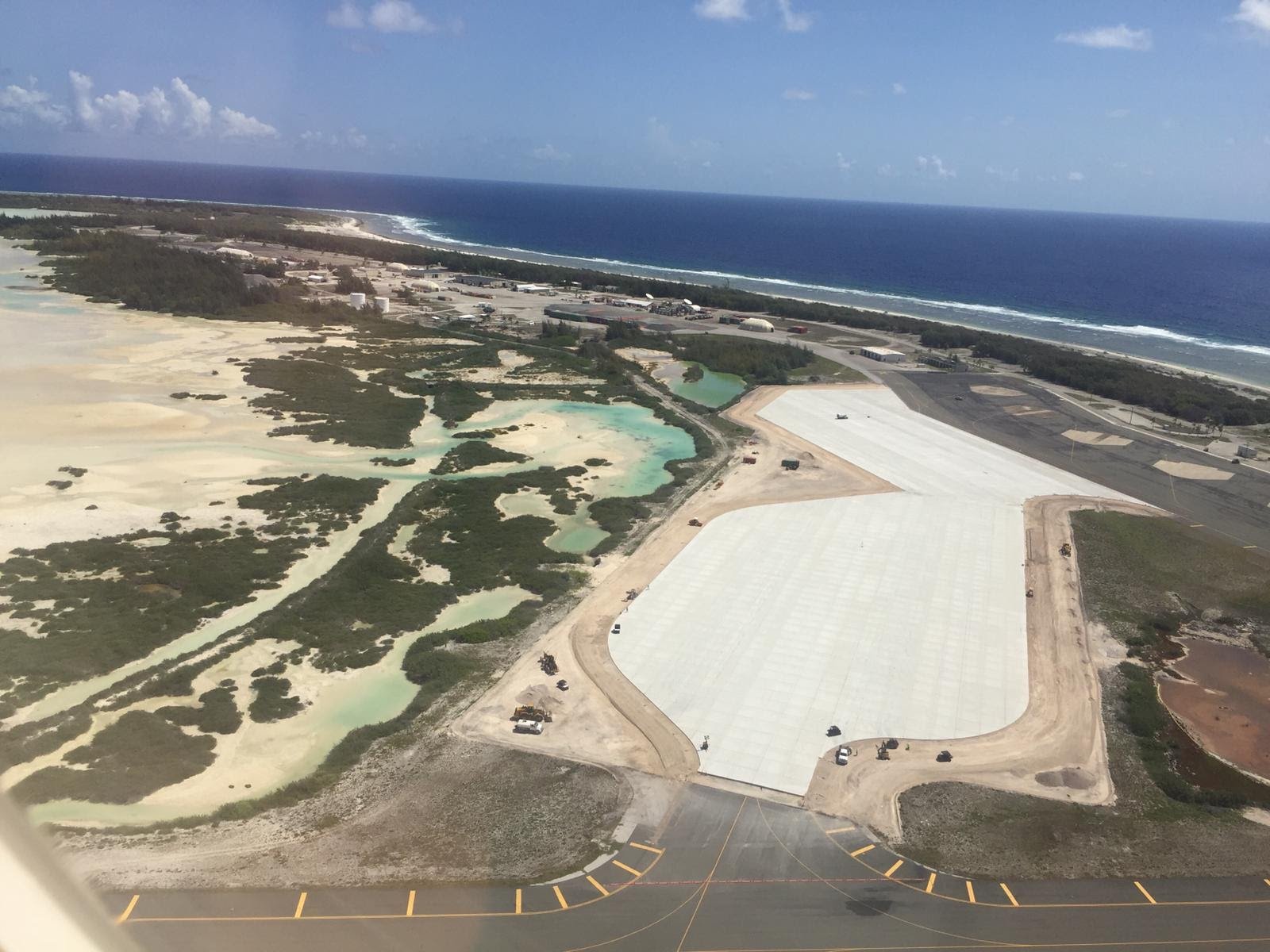